Hi everyone.
I would like to consult for a blower that was recently repaired? I would appreciate any help on this.
Attached document is my initial investigation of the blower and hopefully you may take time to read this. On the last pages of this presentation are only my suspicion. I haven't included the integrity of the Allen cap screws but would also send this for a shear test and tensile test for verification. This blower is driven by a 250hp motor/4160voltage. Blower speed is 1565rpm. I would really need any expert advice on this matter.
I would appreciate any help on this please.
Thank you very much.
Sincerely,
Whispair guy (fmcseals)
I would like to consult for a blower that was recently repaired? I would appreciate any help on this.
Attached document is my initial investigation of the blower and hopefully you may take time to read this. On the last pages of this presentation are only my suspicion. I haven't included the integrity of the Allen cap screws but would also send this for a shear test and tensile test for verification. This blower is driven by a 250hp motor/4160voltage. Blower speed is 1565rpm. I would really need any expert advice on this matter.
I would appreciate any help on this please.
Thank you very much.
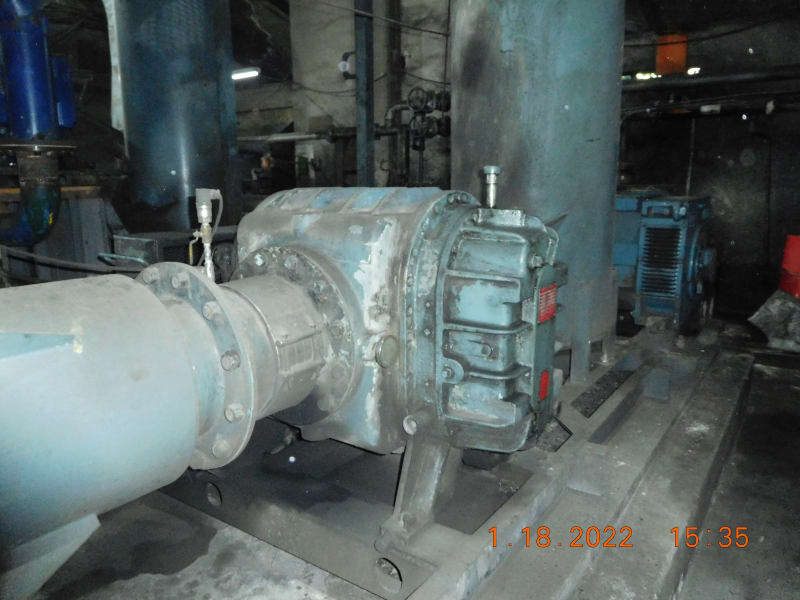
Sincerely,
Whispair guy (fmcseals)