BragiBaldursson
Member
Can an FEA expert with access to Abaqus/Nastran see if they can match this simple problem of a single shear joint with riveted fasteners. Fasteners are to be modeled as beam elements (circular) tied to the doubler and skin (1 inch apart). Fastener diameter is calculated from Tom Swift´s fastener flexibility to be 0.406 inches in diameter and fastener length of 1 inch. I would like to know if the hand calculations compare well with FEM results for the bearing and bypass loads.
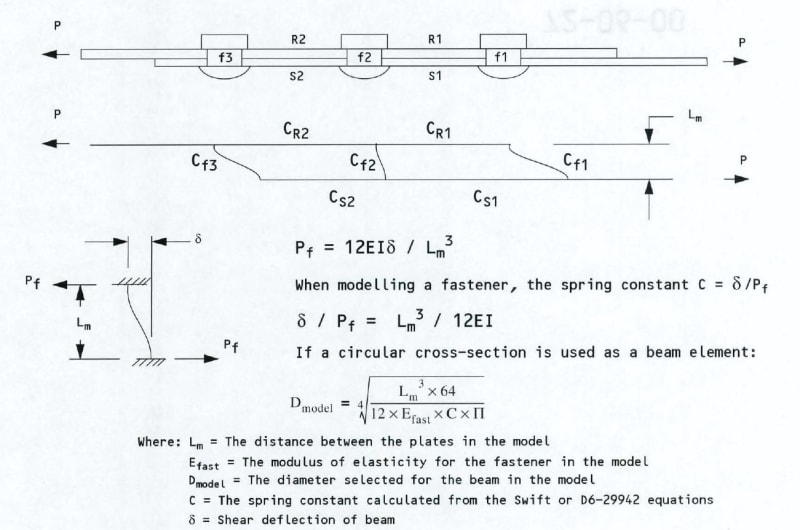
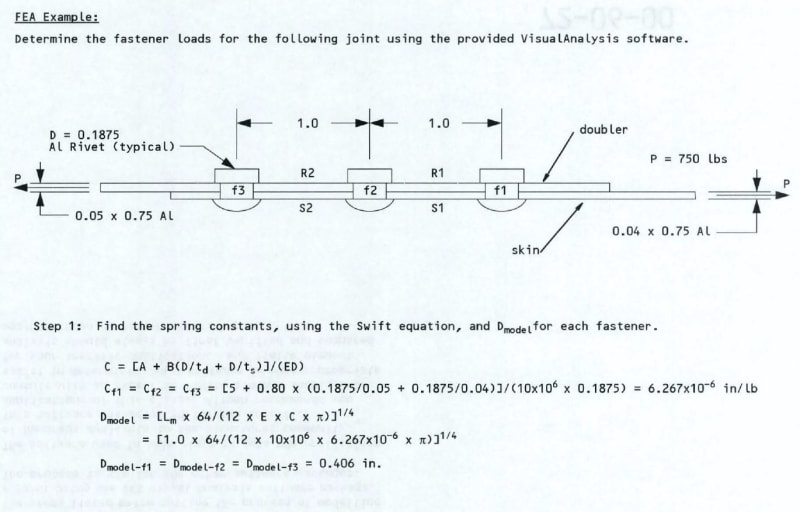
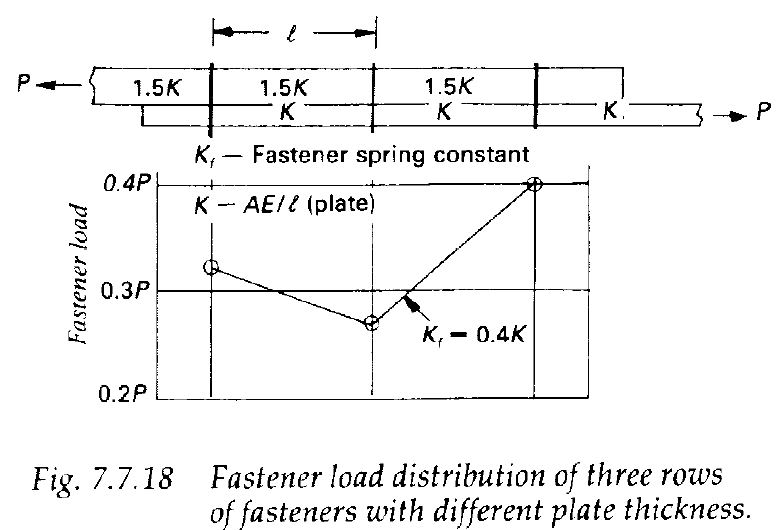
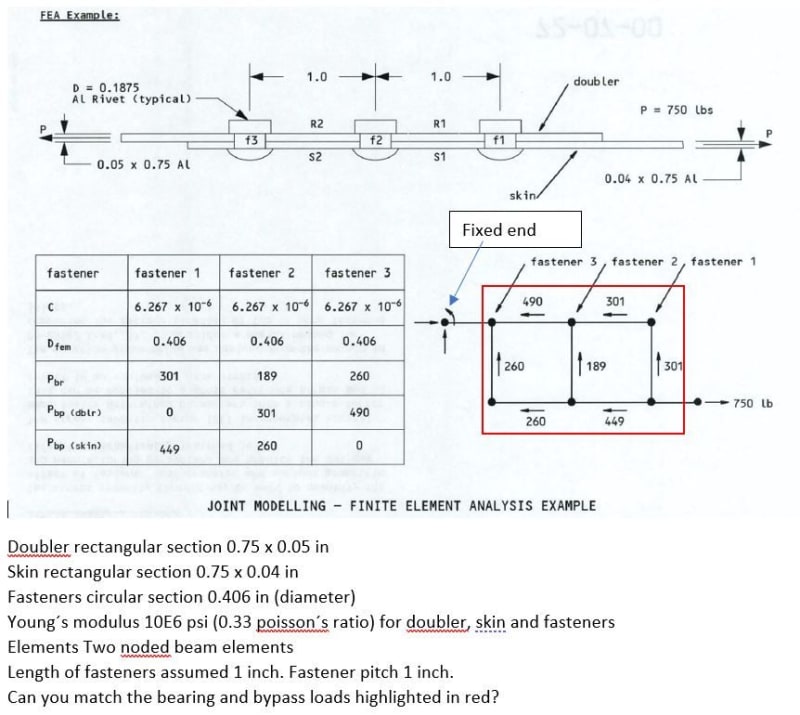