francis_intano
Structural
Hello!
Can someone help me clarify about triangular plate stresses in STAAD. i know that this guide exist (see below)
but how would I interpret this in a triangular elements? something like this:
Thanks a lot btw.
Can someone help me clarify about triangular plate stresses in STAAD. i know that this guide exist (see below)
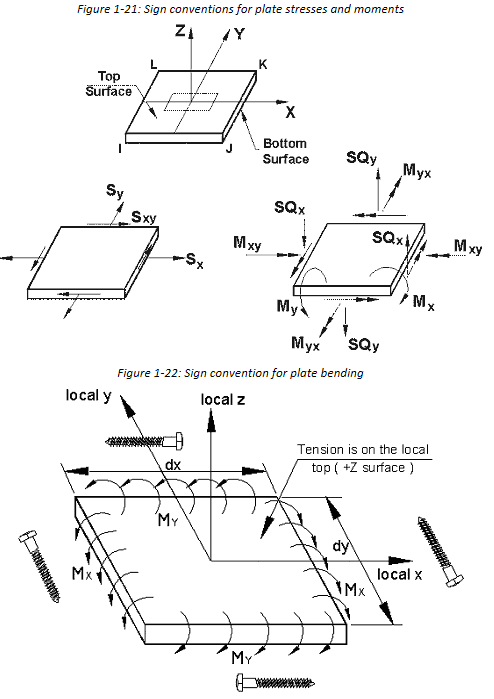
but how would I interpret this in a triangular elements? something like this:
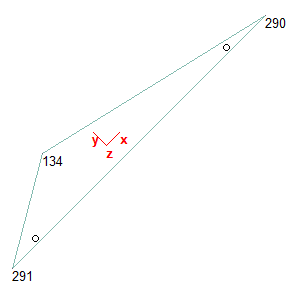
Thanks a lot btw.