WillingToLearn
Student
Hello everyone,
I am trying to model a fiber reinforced part:
This is a single part with internal boundaries. The white/grey area represent cohesive elements. Now I am wondering how I can deal with compressive failure of the cohesive elements.
Once the cohesive elements fail, there is no more connection between the fiber (green) and the matrix (red). The Abaqus manual suggests contact conditions, but for some reason I can't apply them to this geometry (the green area is not considered a separate surface and therefore can't be selected).
How do I best deal with the compressive failure of the cohesive elements?
Kind regards
Mike
I am trying to model a fiber reinforced part:
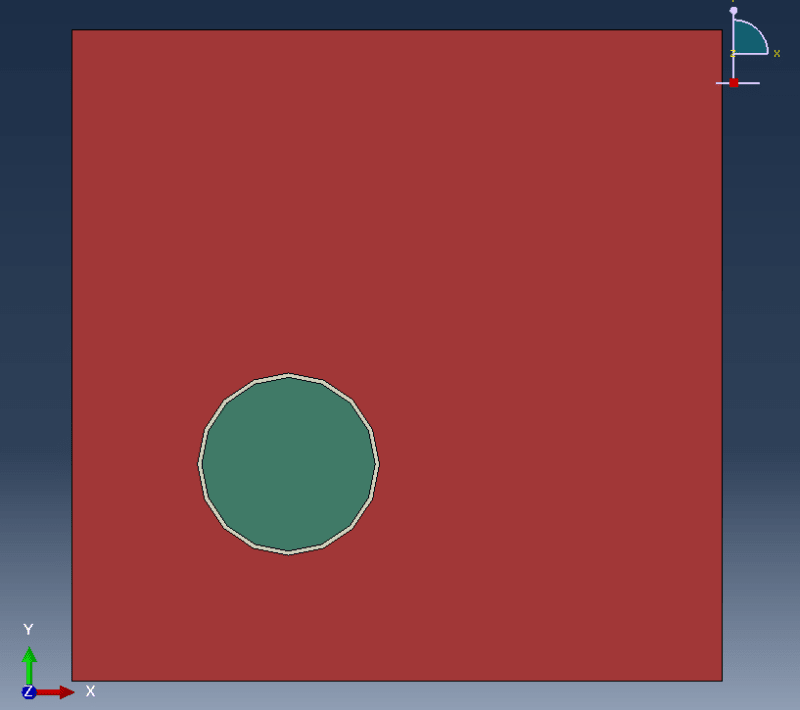
This is a single part with internal boundaries. The white/grey area represent cohesive elements. Now I am wondering how I can deal with compressive failure of the cohesive elements.
Once the cohesive elements fail, there is no more connection between the fiber (green) and the matrix (red). The Abaqus manual suggests contact conditions, but for some reason I can't apply them to this geometry (the green area is not considered a separate surface and therefore can't be selected).
How do I best deal with the compressive failure of the cohesive elements?
Kind regards
Mike