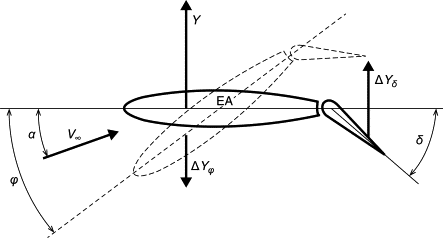
We want to minimize the gap between the control surface & fixed surface of the wing. Currently, our Control surface leading edge has round shape as shown above and the wing shroud (or closeout shroud connecting the top & bottom skins) is also similarly shaped. Our control surface acts as an elevator and hence deflects both upward and downward. We have noticed that in downward deflection, the gap between the wing and control surface grows large enough to affect performance. This issue is further exacerbated by large twists that exists towards the tip of the wing.
Since it is a conceptual study, I am free to modify the shape of control surface LE and also corresponding shroud. Just looking for some ideas on the same. Would appreciate any pointers folks.