Eugene Pavlov
Mechanical
I have a stiffened panel that looks like this:
This panel is under shear:
All sides of the panel are pinned. Txy - is distributed shear load.
Which constraints should I set to simulate stiffened panel under pure shear?
[pre]
As for me I did this (but don't know is it good approach):
Constraints:
Tx Ty Tz Rx Ry Rz
Left: - - x - - x
Right: - - x - - x
Top: - - x - - x
Bottom: - - x - - x
A: x x - - - -
D: - x - - - -
Where: Tx, Ty, Tz - translational degrees of freedom
Rx, Ry, Rz - rotational degrees of freedom
'-' denotes free degree of freedom
'x' denotes fixed degree of freedom
A - left bottom node // B ---- C
D - right bottom node // | |
// A ---- D
Then I set distributed load on each side in appropriate direction.
[/pre]
So which kind of constraints would you advice?
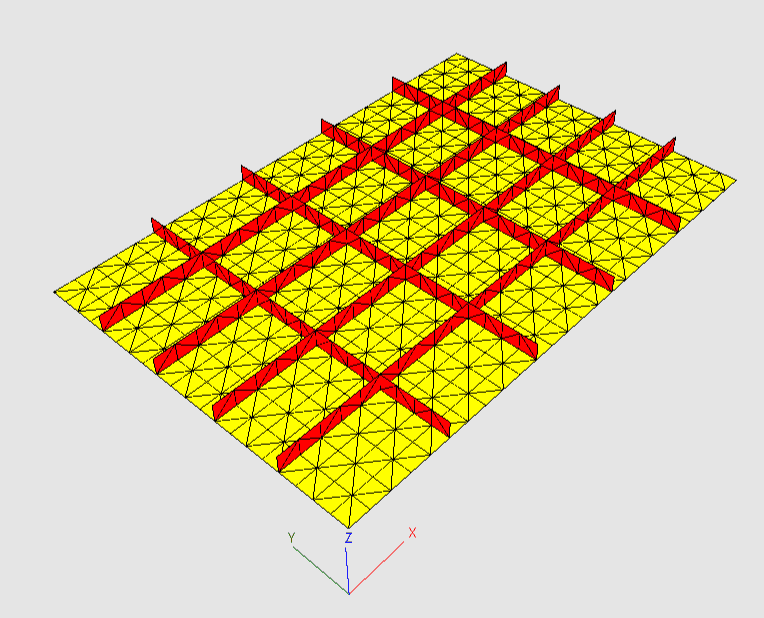
This panel is under shear:
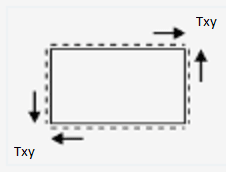
All sides of the panel are pinned. Txy - is distributed shear load.
Which constraints should I set to simulate stiffened panel under pure shear?
[pre]
As for me I did this (but don't know is it good approach):
Constraints:
Tx Ty Tz Rx Ry Rz
Left: - - x - - x
Right: - - x - - x
Top: - - x - - x
Bottom: - - x - - x
A: x x - - - -
D: - x - - - -
Where: Tx, Ty, Tz - translational degrees of freedom
Rx, Ry, Rz - rotational degrees of freedom
'-' denotes free degree of freedom
'x' denotes fixed degree of freedom
A - left bottom node // B ---- C
D - right bottom node // | |
// A ---- D
Then I set distributed load on each side in appropriate direction.
[/pre]
So which kind of constraints would you advice?