John_Hoekstra
Structural
Good day people
I have a question about a Variable frequency drive and I hope somebody could help me with it. In my free time, I try to get more knowledge about electric drives. I stumbled on a question that I couldn't find directly an answer on it. The question is: Do you need a buck converter after your inverter if you have different source voltages? For example, you have a mobile unit and you want to be able to make it available for 690 400, etc.
Thanking you in Advance
With regards,
John
I have a question about a Variable frequency drive and I hope somebody could help me with it. In my free time, I try to get more knowledge about electric drives. I stumbled on a question that I couldn't find directly an answer on it. The question is: Do you need a buck converter after your inverter if you have different source voltages? For example, you have a mobile unit and you want to be able to make it available for 690 400, etc.
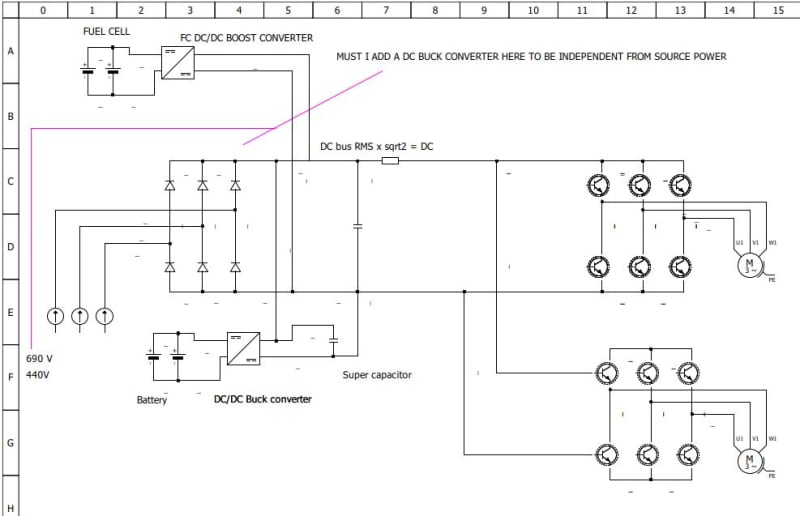
Thanking you in Advance
With regards,
John