All,
I was looking at some techniques to simplify Shell mesh structures.
As an example, I have a door edge with a bolted brace as shown. The brace is 0.25" while the steel structure is 10 gauge steel.
Can this be simplified to a 2D mesh with two separate mid surfaces
OR
A single shell mesh with split surface and different plate thickness?
Thank you!
I was looking at some techniques to simplify Shell mesh structures.
As an example, I have a door edge with a bolted brace as shown. The brace is 0.25" while the steel structure is 10 gauge steel.
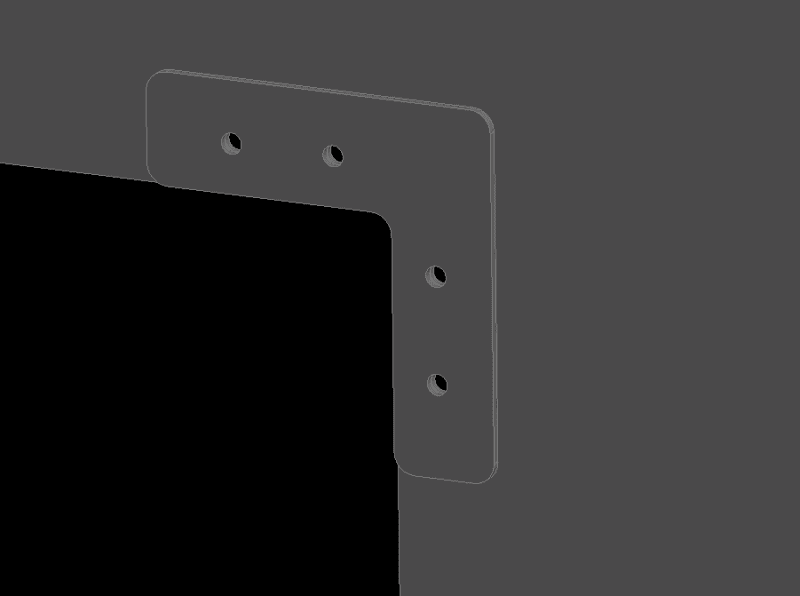
Can this be simplified to a 2D mesh with two separate mid surfaces
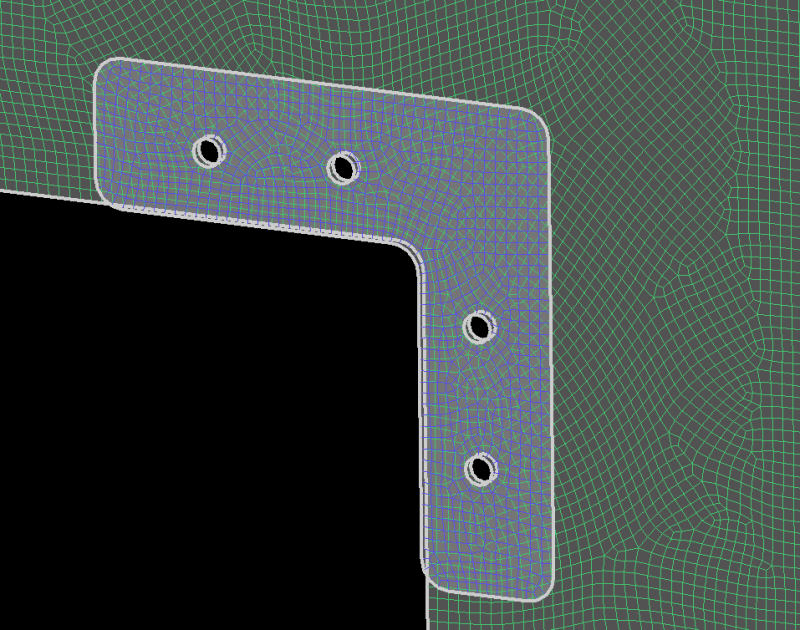
OR
A single shell mesh with split surface and different plate thickness?
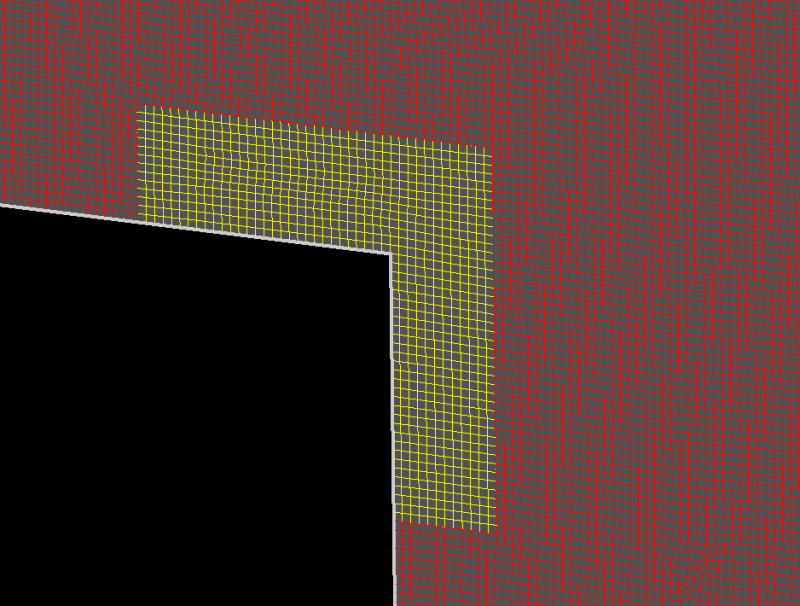
Thank you!