VaidehiChennubhotla
Mechanical
I have a shell structure and solid structure with merged nodes (Nodal equivalence) in Abaqus. The thickness of the shell structure is 1.5 mm . What should be the section thickness that I should assign in *section ?Generally we select the mid-surface for assigning the section thickness. I dont want the shell structure to penetrate into the solid structure as I have merged the nodes.
Red is the shell
White is Solid
Green is solid
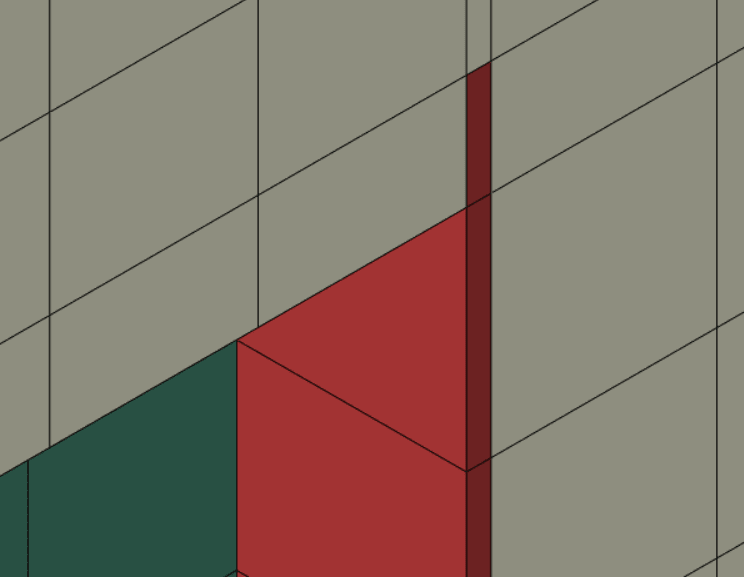
Red is the shell
White is Solid
Green is solid