VaidehiChennubhotla
Mechanical
Hi,
A Hyperelastic material model was used for compression test on a 50x50x50 mm block. The compression test data (FS curve) was overlaid on the CAE data. It fails to replicate the test data behavior miserably, shown in below picture. Hyperelastic material in general has uniaxial test data Nominal Stress, Nominal Strain and field variable. As I understand tensile test data is used twice and a shear field variable and shear failure criterion is given to show when it fails. Please correct me if I am wrong. I am having difficulty to match the CAE data to Test data. What can be done to the Hyperelastic material card, to make it match with test data? Any help would be greatly appreciated.
Regards,
Vaidehi
A Hyperelastic material model was used for compression test on a 50x50x50 mm block. The compression test data (FS curve) was overlaid on the CAE data. It fails to replicate the test data behavior miserably, shown in below picture. Hyperelastic material in general has uniaxial test data Nominal Stress, Nominal Strain and field variable. As I understand tensile test data is used twice and a shear field variable and shear failure criterion is given to show when it fails. Please correct me if I am wrong. I am having difficulty to match the CAE data to Test data. What can be done to the Hyperelastic material card, to make it match with test data? Any help would be greatly appreciated.
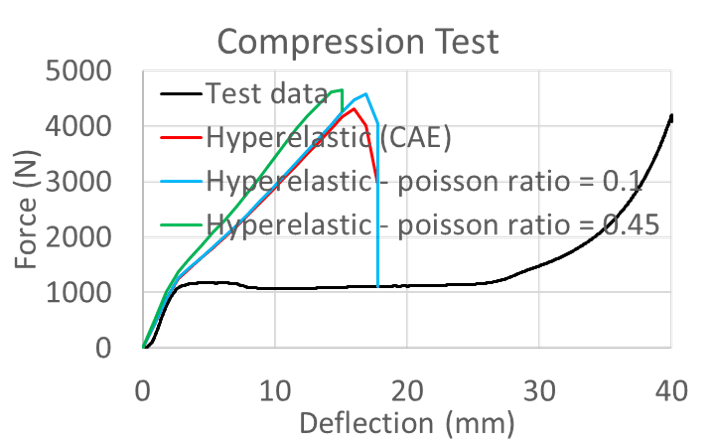
Regards,
Vaidehi