Hello all,
I have a question, I want to solve this problem using the same procedure as SP17 but once I'm done and want to verify my answer and find the column axial load capacity it comes out as inadequate. I'm aware if i dont multiply by 0.65 and 0.8 and rather use phi = 0.7 it comes at at the borderline. but how did aci solve it like that in their design aid? am i missing something?
so is it correct like that at 4% reinf? please help
my problem:
used interaction diagrams:
I have a question, I want to solve this problem using the same procedure as SP17 but once I'm done and want to verify my answer and find the column axial load capacity it comes out as inadequate. I'm aware if i dont multiply by 0.65 and 0.8 and rather use phi = 0.7 it comes at at the borderline. but how did aci solve it like that in their design aid? am i missing something?
so is it correct like that at 4% reinf? please help
my problem:
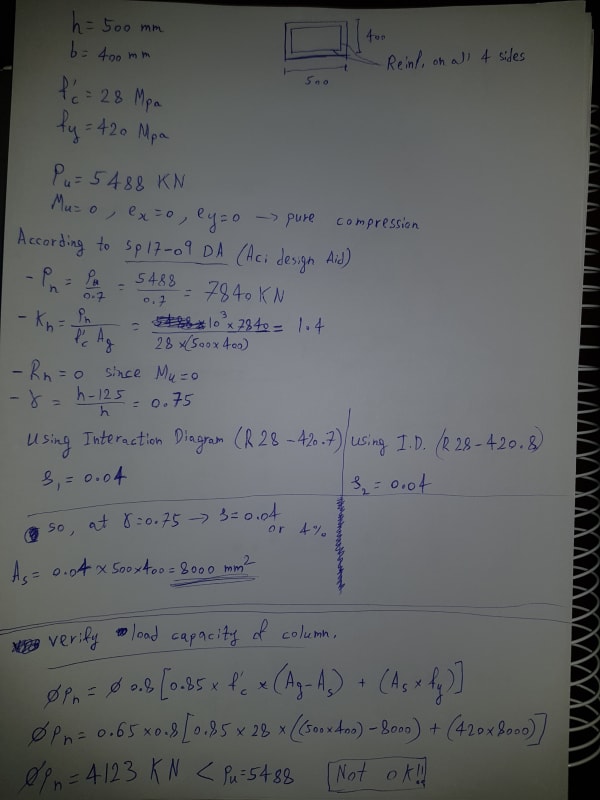
used interaction diagrams:
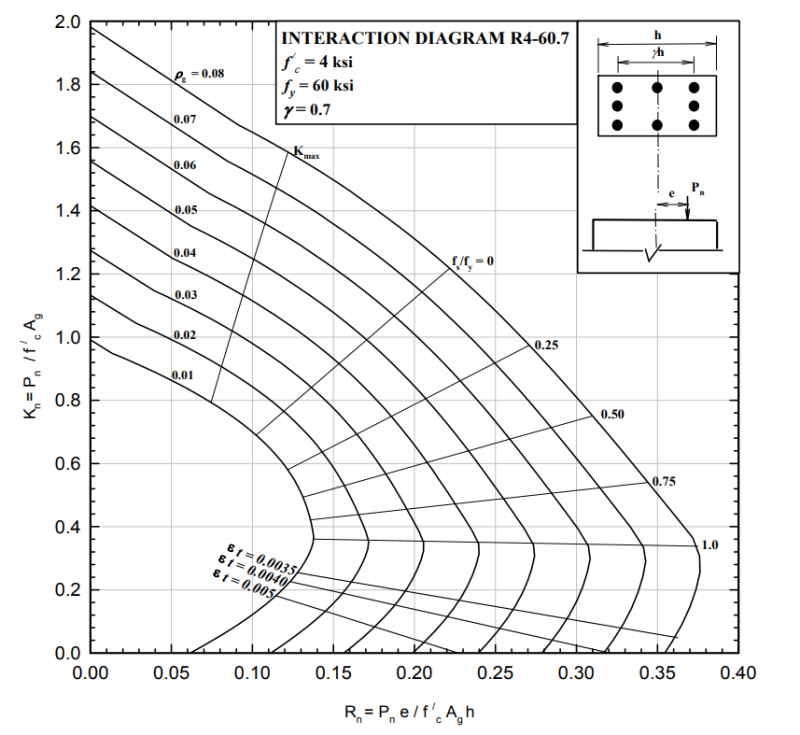
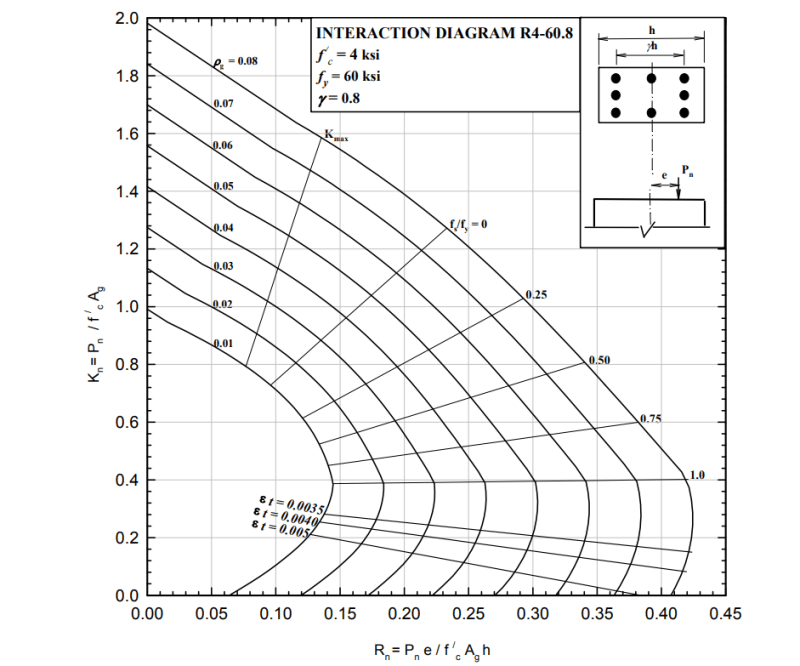