Hi,
Is there any rational design method for anchoring bars by welding them onto horizontal anchor bars and/or bearing plates? Alternatively, is there any good design reference that anyone could recommend?
We know it obviously works (else corbels would be failing everywhere), but I'm searching for some explanation on the design parameters beyond the prescriptive "weld to a transverse weld of equal size or provide suitable anchor".
I'm referring to the weld detail typically used on corbels in which the tension steel is welded to a horizontal anchor bars or bearing plates, such as the detail shown below.
I'm particularly interested in the detail shown below, when welding to bearing plates and/or embedded angles. I would imagine the plate would require some sort of shear connector to be effective when in this orientation, since I doubt there is much of a bond between the concrete and the plate to anchor the bar effectively. However, I haven't been able to find any example showing the sizing of such a part; the dapped beam design examples I've found so far typically skip the sizing of the bearing plate/angle.
Opinions?
Is there any rational design method for anchoring bars by welding them onto horizontal anchor bars and/or bearing plates? Alternatively, is there any good design reference that anyone could recommend?
We know it obviously works (else corbels would be failing everywhere), but I'm searching for some explanation on the design parameters beyond the prescriptive "weld to a transverse weld of equal size or provide suitable anchor".
I'm referring to the weld detail typically used on corbels in which the tension steel is welded to a horizontal anchor bars or bearing plates, such as the detail shown below.
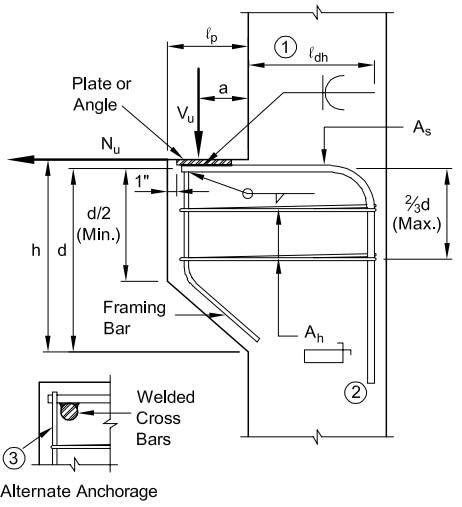
I'm particularly interested in the detail shown below, when welding to bearing plates and/or embedded angles. I would imagine the plate would require some sort of shear connector to be effective when in this orientation, since I doubt there is much of a bond between the concrete and the plate to anchor the bar effectively. However, I haven't been able to find any example showing the sizing of such a part; the dapped beam design examples I've found so far typically skip the sizing of the bearing plate/angle.
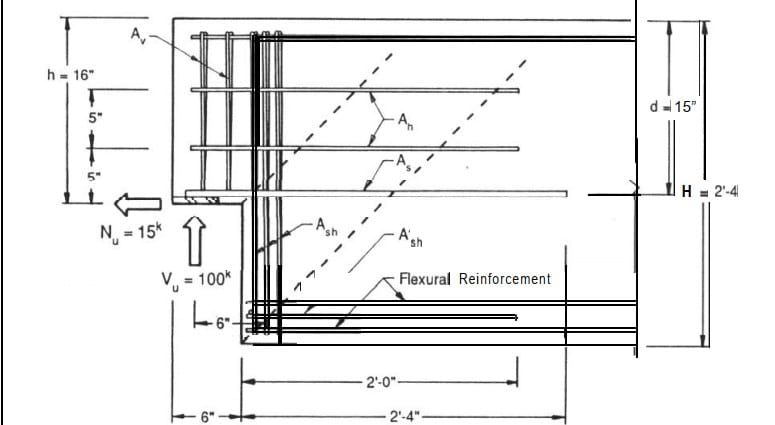
Opinions?