JAE
Structural
- Jun 27, 2000
- 15,587
Similar to the condition described in this thread: thread256-415768
I have a property line column and need to design the footing under it.
I'm familiar with the design of these things - my specific question here relates to the soil stress under the footing.
Per KootK's sketch below (from the referenced thread) there is an assumption made that the soil stress under the set-back footing (the left footing in the image) is uniform.
However, in reality the footing is essentially fixed to the strap beam and in a sense it is "fixed" to the soil - i.e. there are numerous soil "springs" supporting this footing so idealizing it as a pin isn't perfectly modeling reality.
With today's software (i.e. RISA Foundation) we can model this concrete configuration and when we do we get a significant gradient of soil stress under the footing closest to the property line.
In most cases, assuming a uniform soil stress results in an intuitively sized footing. But if we assume a soil-spring behavior, we get much larger soil stresses resulting in very large footings.
When a geotechnical engineer provides us with an allowable soil bearing pressure, it is assumed that this is generally for simply, uniformly loaded pad footings.
BUT.....
1. Soil isn't really linear is it? i.e. springs are only general approximations of soil behavior
2. Can the maximum pressure at the footing toe exceed the general allowable values a geotechnical engineer provides?
3. Thousands of strap type footings have been built in the past assuming uniform bearing - they seem to apparently work.
4. Does the soil somehow allow minimal rotation and still provide a general uniform bearing anyway...despite what our FEA foundation analysis suggests?
Thoughts and help please!
Check out Eng-Tips Forum's Policies here:
faq731-376
I have a property line column and need to design the footing under it.
I'm familiar with the design of these things - my specific question here relates to the soil stress under the footing.
Per KootK's sketch below (from the referenced thread) there is an assumption made that the soil stress under the set-back footing (the left footing in the image) is uniform.
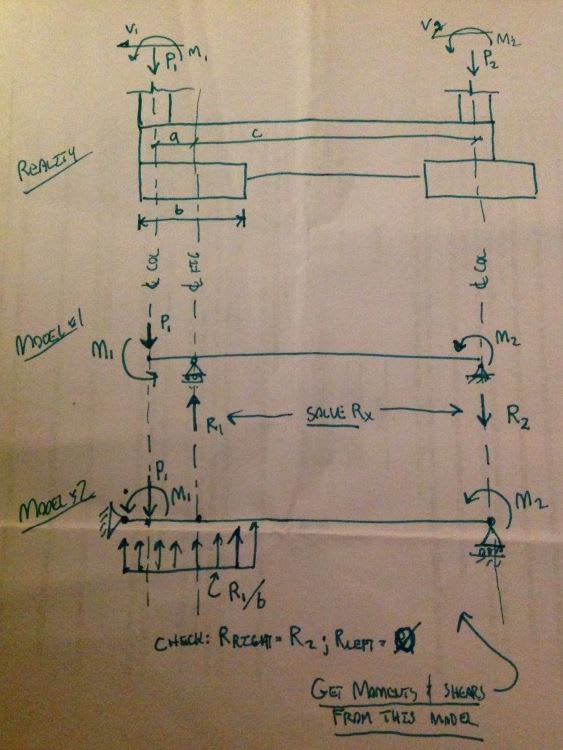
However, in reality the footing is essentially fixed to the strap beam and in a sense it is "fixed" to the soil - i.e. there are numerous soil "springs" supporting this footing so idealizing it as a pin isn't perfectly modeling reality.
With today's software (i.e. RISA Foundation) we can model this concrete configuration and when we do we get a significant gradient of soil stress under the footing closest to the property line.
In most cases, assuming a uniform soil stress results in an intuitively sized footing. But if we assume a soil-spring behavior, we get much larger soil stresses resulting in very large footings.
When a geotechnical engineer provides us with an allowable soil bearing pressure, it is assumed that this is generally for simply, uniformly loaded pad footings.
BUT.....
1. Soil isn't really linear is it? i.e. springs are only general approximations of soil behavior
2. Can the maximum pressure at the footing toe exceed the general allowable values a geotechnical engineer provides?
3. Thousands of strap type footings have been built in the past assuming uniform bearing - they seem to apparently work.
4. Does the soil somehow allow minimal rotation and still provide a general uniform bearing anyway...despite what our FEA foundation analysis suggests?
Thoughts and help please!
Check out Eng-Tips Forum's Policies here:
faq731-376