Hi,
First time poster - hope this isn't off base.
I'm looking for a manufacturer for the product pictured below. I need to know what TYPE of manufacturing methods could be used to make this part (injection molding, extrusion, thermoforming, etc.)
It is about 21" (533mm) in diameter and about .040-.080" (1-2mm) in cross section. I don't have a material in mind. It should be roughly 70-90D, tough, and capable of stretching at least 2% without permanent deformation.
Suggestions are appreciated.
First time poster - hope this isn't off base.
I'm looking for a manufacturer for the product pictured below. I need to know what TYPE of manufacturing methods could be used to make this part (injection molding, extrusion, thermoforming, etc.)
It is about 21" (533mm) in diameter and about .040-.080" (1-2mm) in cross section. I don't have a material in mind. It should be roughly 70-90D, tough, and capable of stretching at least 2% without permanent deformation.
Suggestions are appreciated.
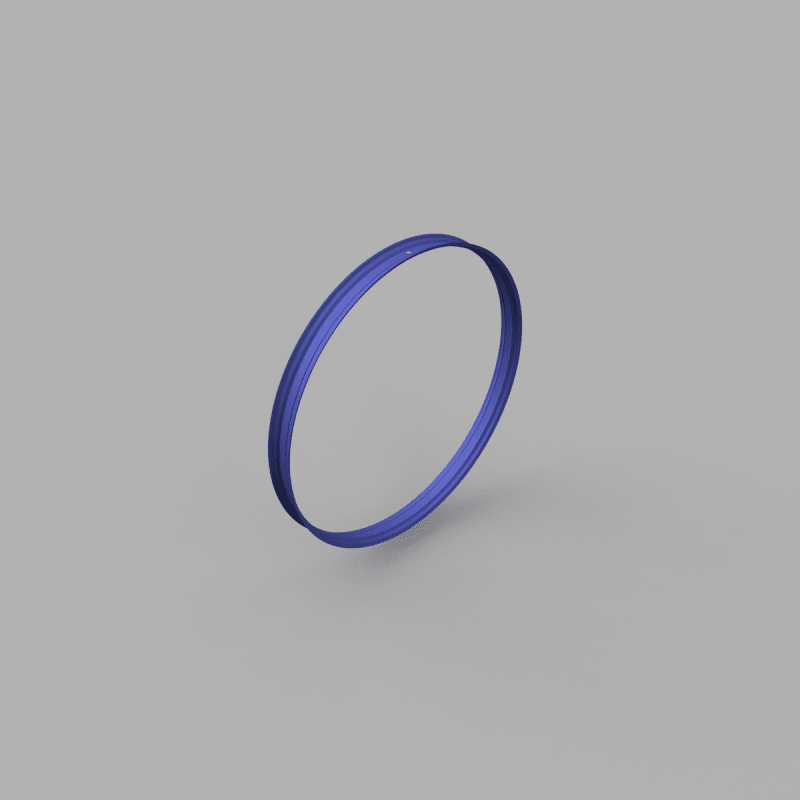
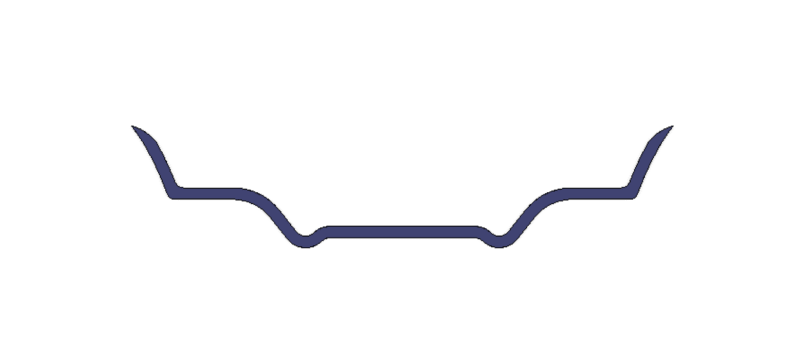