I am trying to validate the strength of the component which operates in a certain frequency range. NX Advanced simulation - SOl 103 Response Dynamics is used to do the simulation. Based on the Mode shapes, I am creating the Frequency Response Event. Now the doubt is, where should I input the damping. The component is made of cast-iron and I would like to give 3% damping.
Following are the two ways, the software allows to feed damping . But which is the correct way?
One for the Mode shape - (Modal Damping)
And other at Material Properties Table : Structural Damping.
Which is the correct way?
Following are the two ways, the software allows to feed damping . But which is the correct way?
One for the Mode shape - (Modal Damping)
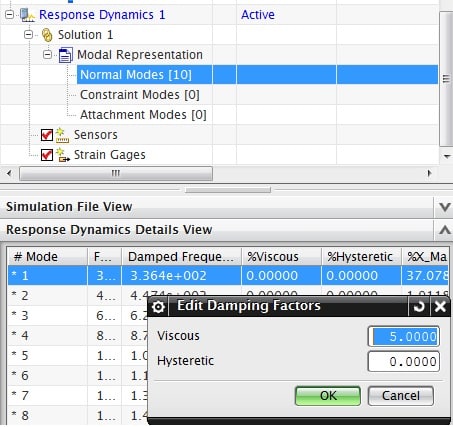
And other at Material Properties Table : Structural Damping.

Which is the correct way?