JAE
Structural
- Jun 27, 2000
- 15,587
We have a project and have come upon a problem - wondering if others have an approach to deal with it.
1. Single story building - generally rectangular in plan with one of the long walls having a jog or offset. There is also a small offset in the short wall near the long wall offset.
2. The building is supported by perimeter load-bearing precast wall panels all around which serve as shear walls as well.
3. The roof is steel joist with metal decking.
4. Wind case perpendicular to long walls.
5. Because of the jog in the long wall, there is a short precast wall segment about 3/4 of the way down the wall.
6. This wall segment acts as an intermediate, short shear wall and with classic tributary wind design attracts a LOT of load.
7. If we model a semi-rigid diaphragm, the shear wall still attracts a lot of load.
8. With the offset in the short wall, the "end wall" of the long rectangular diaphragm has two separate shear walls - an inner wall and an outer wall.
9. The inner wall attracts a lot of the load and the outer wall is actually attracting a small amount of load in the opposite direction due to bending/deflection in the diaphragm.
10. We have included spring supports to model the shear wall stiffnesses as well - this doesn't help all that much.
Is there any approach to analysis where you can minimize the load in these short segment offset shear walls? We thought of having a slip connection between wall and diaphragm to release the shear from it but that is very complicated and of questionable efficacy.
Check out Eng-Tips Forum's Policies here:
faq731-376
1. Single story building - generally rectangular in plan with one of the long walls having a jog or offset. There is also a small offset in the short wall near the long wall offset.
2. The building is supported by perimeter load-bearing precast wall panels all around which serve as shear walls as well.
3. The roof is steel joist with metal decking.
4. Wind case perpendicular to long walls.
5. Because of the jog in the long wall, there is a short precast wall segment about 3/4 of the way down the wall.
6. This wall segment acts as an intermediate, short shear wall and with classic tributary wind design attracts a LOT of load.
7. If we model a semi-rigid diaphragm, the shear wall still attracts a lot of load.
8. With the offset in the short wall, the "end wall" of the long rectangular diaphragm has two separate shear walls - an inner wall and an outer wall.
9. The inner wall attracts a lot of the load and the outer wall is actually attracting a small amount of load in the opposite direction due to bending/deflection in the diaphragm.
10. We have included spring supports to model the shear wall stiffnesses as well - this doesn't help all that much.
Is there any approach to analysis where you can minimize the load in these short segment offset shear walls? We thought of having a slip connection between wall and diaphragm to release the shear from it but that is very complicated and of questionable efficacy.
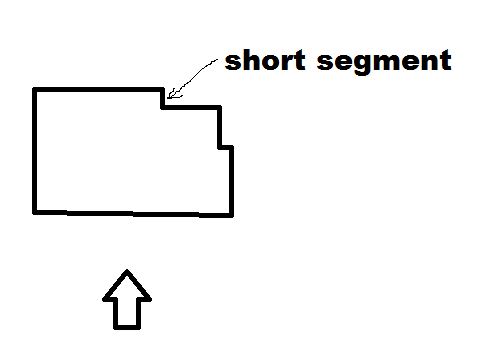
Check out Eng-Tips Forum's Policies here:
faq731-376