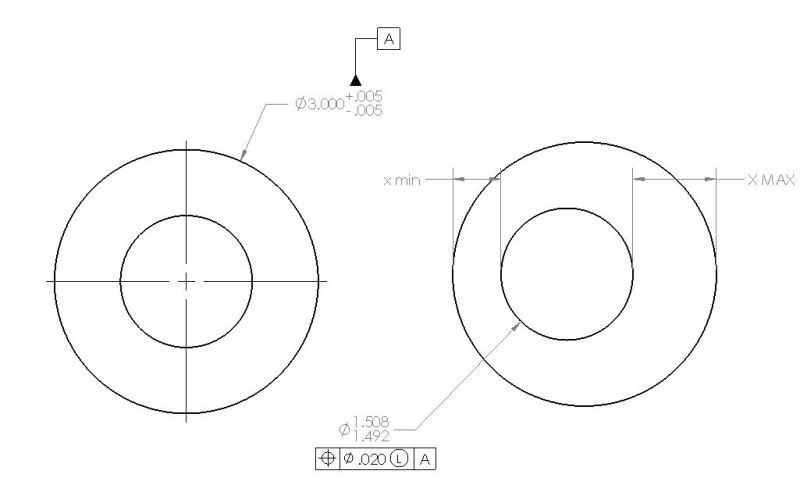
New on the form. Glad I found this site.
Story: shown washer received from supplier, measured by QE department found non-conforming, disposition rejected.
Supplier yelling the parts meet the print.
Inspectors using X min and X max methods to determine the worst case.
Question: what would be the theoretical values (absolute minimum and absolute maximum)?
Supplier states:
x min.: .7285
X Max.: .7745
QE/Inspectors :
X min.: .7335
X Max.: .7665.
Parts measured on CMM are closer to the supplier values (and obviously they are defending their calculated numbers)
Algorithms used: maximum inscribed and minimum circumscribed circles (not LSQ)
Which theoretical values you agree with (if any)? Supplier or QE/Inspector?