EngineerMickeyMouse
Structural
Hi All,
Today my questions consider linear dynamics. Please see them below.
1.Could you please tell me should one expect results from Frequency Response to be somehow corresponding with results from Transient Stress analysis?
2. If yes, please let me know the relationship.
3. What output/result difference is important between Transient Stress Modal Superposition and Transient Stress Direct Integration?
Some insights of my analysis (and description of the figures attached):
As per benchmark I have calculated Natural Frequencies and used them for Frequency Response to readout max displacements for my structure for resonance frequencies. Afterwards I have performed Transient Stress Modal Superposition and plotted max Displacement vs Time which is showing that analysis in first seconds sees max displacements smaller than max values recorded at Frequency Response, second observation is that Modal Superposition is converging for 1.077 mm, while from Static Linear max displacement was 0.25 mm. Next analysis performed was Transient Stress Direct Integration, where 1st observation was max displacements are smaller than max values recorded at Frequency Response, second observation is that Direct Integration is converging for 0.25 mm which corresponds well to the Static Linear. Should I expect to see max displacement values as per Frequency Response, in the Transient Stress analysis?
Today my questions consider linear dynamics. Please see them below.
1.Could you please tell me should one expect results from Frequency Response to be somehow corresponding with results from Transient Stress analysis?
2. If yes, please let me know the relationship.
3. What output/result difference is important between Transient Stress Modal Superposition and Transient Stress Direct Integration?
Some insights of my analysis (and description of the figures attached):
As per benchmark I have calculated Natural Frequencies and used them for Frequency Response to readout max displacements for my structure for resonance frequencies. Afterwards I have performed Transient Stress Modal Superposition and plotted max Displacement vs Time which is showing that analysis in first seconds sees max displacements smaller than max values recorded at Frequency Response, second observation is that Modal Superposition is converging for 1.077 mm, while from Static Linear max displacement was 0.25 mm. Next analysis performed was Transient Stress Direct Integration, where 1st observation was max displacements are smaller than max values recorded at Frequency Response, second observation is that Direct Integration is converging for 0.25 mm which corresponds well to the Static Linear. Should I expect to see max displacement values as per Frequency Response, in the Transient Stress analysis?
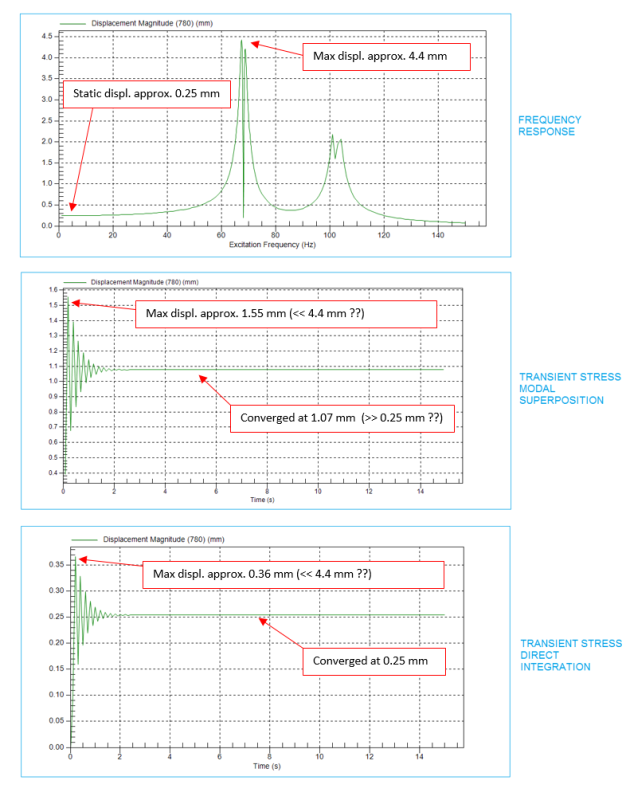