Hi there,
We are 3D printing some plastic capsules with laser technology in Shapeways (Polyamide 2200 material). We want to make a hole of 1 mm and plug 4 small optical fibers.
The idea is making a ferrule for the fibers. We glue it and then we polish everything. Then we plug it in the hole of the capsule.
How can we make a system that makes sure the ferrule will stay in the hole? The ferrule should also be made in plastic (maybe PEEK?).
The quality of the printed ferrules (down here some pictures) doesn't look so good. We machine the hole ourselves (after printing).
Thank you
We are 3D printing some plastic capsules with laser technology in Shapeways (Polyamide 2200 material). We want to make a hole of 1 mm and plug 4 small optical fibers.
The idea is making a ferrule for the fibers. We glue it and then we polish everything. Then we plug it in the hole of the capsule.
How can we make a system that makes sure the ferrule will stay in the hole? The ferrule should also be made in plastic (maybe PEEK?).
The quality of the printed ferrules (down here some pictures) doesn't look so good. We machine the hole ourselves (after printing).
Thank you
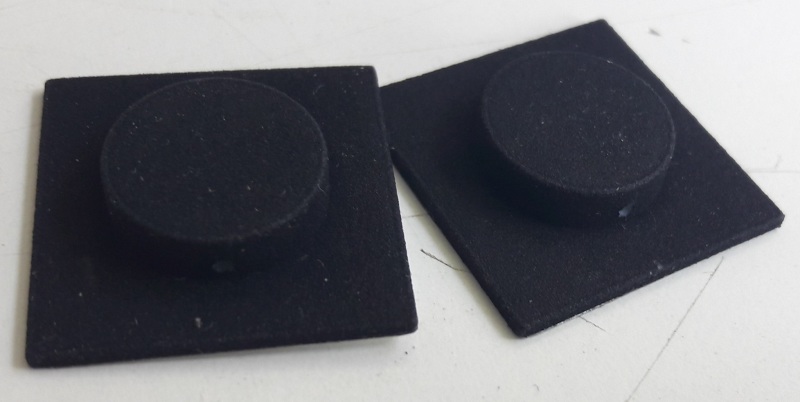

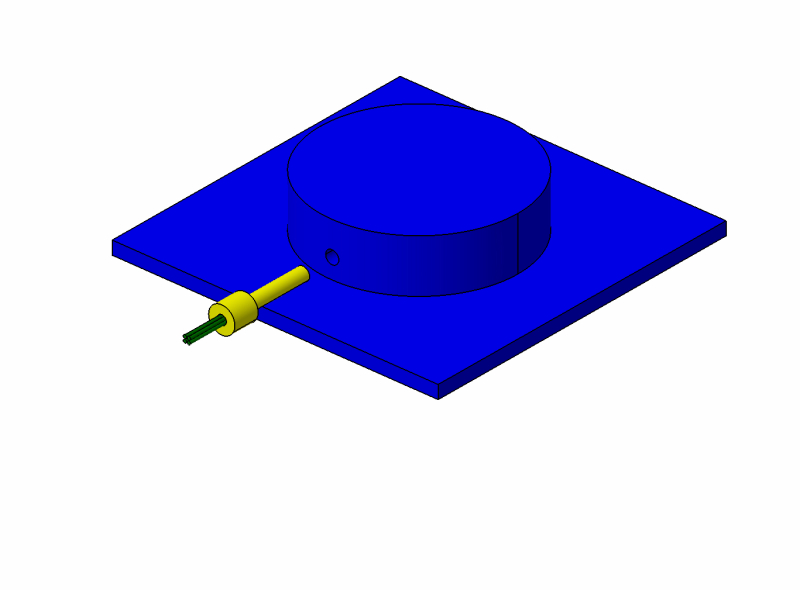
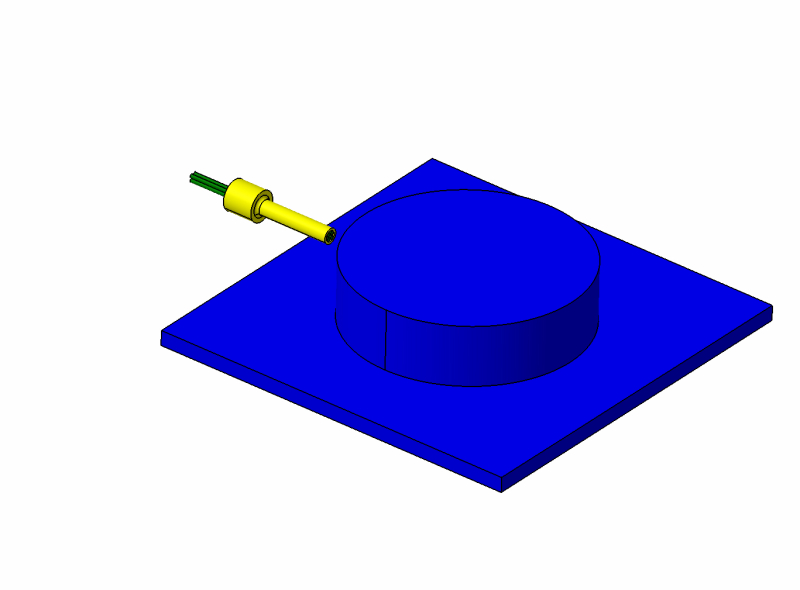
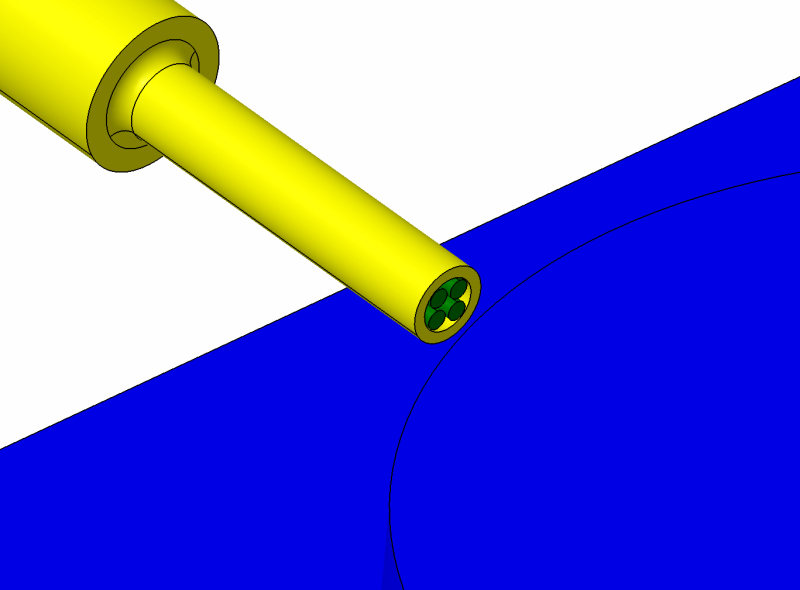