We're working on packaging an industrial product where we will have to meet UL Type 12 and IP54. I've seen some products where they have made the enclosure out of gasketed sheet-metal without welding. One place we have trouble with is getting the corners to seal up without resorting to welding.
Something we've seen uses a feature like this:
The small web of material formed provides a gasket sealing surface at the corner. Does anyone have experience at making a feature like this? I'm suspecting that it could be done on a press brake with a special tooth that has a recess to form the web around the corner.
Thanks in advance,
Matthew
Something we've seen uses a feature like this:
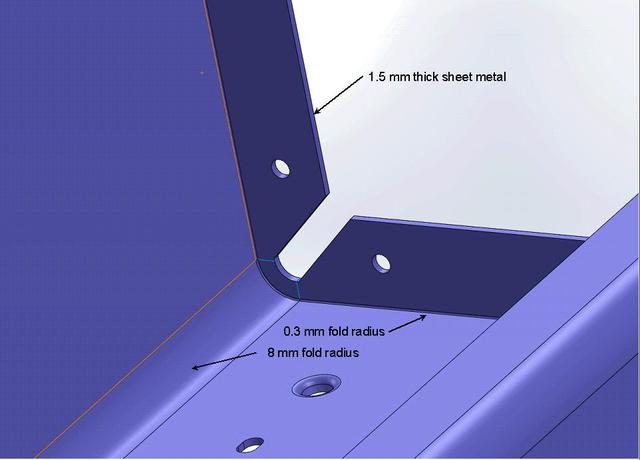
The small web of material formed provides a gasket sealing surface at the corner. Does anyone have experience at making a feature like this? I'm suspecting that it could be done on a press brake with a special tooth that has a recess to form the web around the corner.
Thanks in advance,
Matthew