-
1
- #1
JohnRwals
Structural
- Jul 8, 2020
- 151
Hello!
P1 and P2 have exactly the same conditions except top, bottom horizontal welding.
I thought P2 could support greater vertical load.
But...
Which one do you think can support greater load? Why?
Thanks!
JW
R
P1 and P2 have exactly the same conditions except top, bottom horizontal welding.
I thought P2 could support greater vertical load.
But...
Which one do you think can support greater load? Why?
Thanks!
JW
R
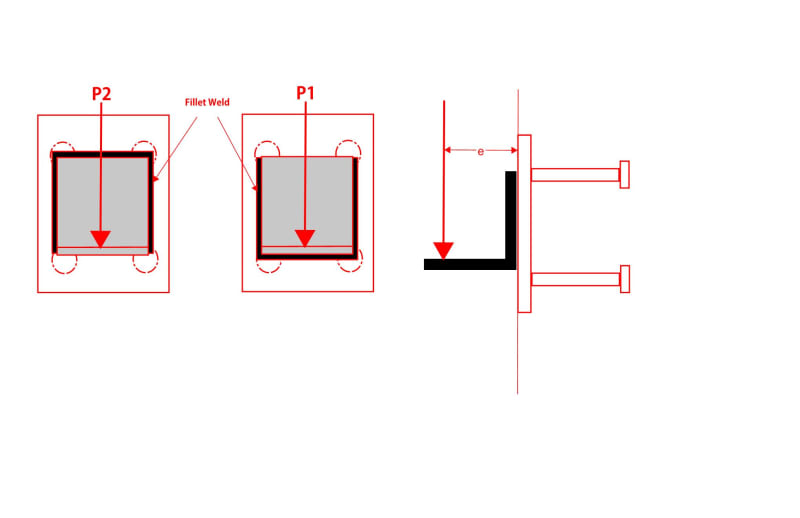