Ussuri
Civil/Environmental
- May 7, 2004
- 1,582
I have a detail (see below) where I have a 250RHS resting on a 150SHS corbel, which is itself attached to a 406CHS.
I am looking at the tubular joint check (RHS brace to CHS chord). I am looking for some guidance into the joint capacity where the incoming brace is eccentric to the chord centreline. I normally use CIDECT for my joint checks. However, CIDECT deals with joints where the centrelines intersect, presumably this is because all the physical testing is based on this arrangement.
API RP2A allows an eccentricity of D/4 (although this is specific for CHS to CHS joints) but offers no guidance if you exceed D/4.
Is anyone aware of any research or guidance on the capacity of tubular joints with an out of plane offset in the incoming brace?
I am looking at the tubular joint check (RHS brace to CHS chord). I am looking for some guidance into the joint capacity where the incoming brace is eccentric to the chord centreline. I normally use CIDECT for my joint checks. However, CIDECT deals with joints where the centrelines intersect, presumably this is because all the physical testing is based on this arrangement.
API RP2A allows an eccentricity of D/4 (although this is specific for CHS to CHS joints) but offers no guidance if you exceed D/4.
Is anyone aware of any research or guidance on the capacity of tubular joints with an out of plane offset in the incoming brace?
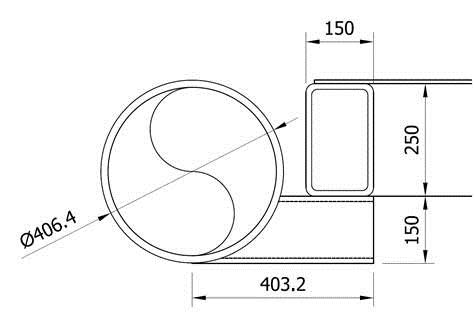