medeek
Structural
- Mar 16, 2013
- 1,104
For gable roof overhangs over 12" in length I generally go with structural outlookers with a dropped top chord on the gable end truss. These outlookers can either be oriented horizontally or vertically. The problem I see with this method of construction is the connection between the roof diaphragm (sheathing) and the gable end truss. Solid 2x blocking between the outlookers is typically called out with some sort of tie for the outlookers to the truss for uplift. The blocking between the outlookers is nailed to the roof sheathing with typical panel edge nailing (8d @ 3",4",6" o/c). In my locale with high wind loads I usually call out overhang roof sheathing nailing at 4" o/c.
The load path problem is the connection between the 2x blocking btw. outlookers and the gable end truss for the resistance of shear in plane with the gable end truss/wall. I haven't really given this too much thought before and my various details don't really give much information on this blocking connections. For instance the recent detail for gable end wall bracing:
I like to use H4 clips on the outlookers, since they are small enough for application to either vert. or horiz. outlookers. However, at lateral load capacity of 165 lbs each it would be hard to rely on just these clips for any significant shear wall loads. The 2x solid blocking will either need additional toe-nailing, sheathing or LTP4 connectors to allow for more shear transfer.
Rather than use a dropped top chord truss I think it would be easier to bump up the depth of the top chord member and then notch out for the outlookers as required. This solves the connection problem described above and would seem like a much stronger connection at this location.
What do you see with residential roofs in your neck of the woods? Are dropped top chord trusses with structural outlookers the norm and if they are how do you deal with them?
A confused student is a good student.
Nathaniel P. Wilkerson, PE
The load path problem is the connection between the 2x blocking btw. outlookers and the gable end truss for the resistance of shear in plane with the gable end truss/wall. I haven't really given this too much thought before and my various details don't really give much information on this blocking connections. For instance the recent detail for gable end wall bracing:
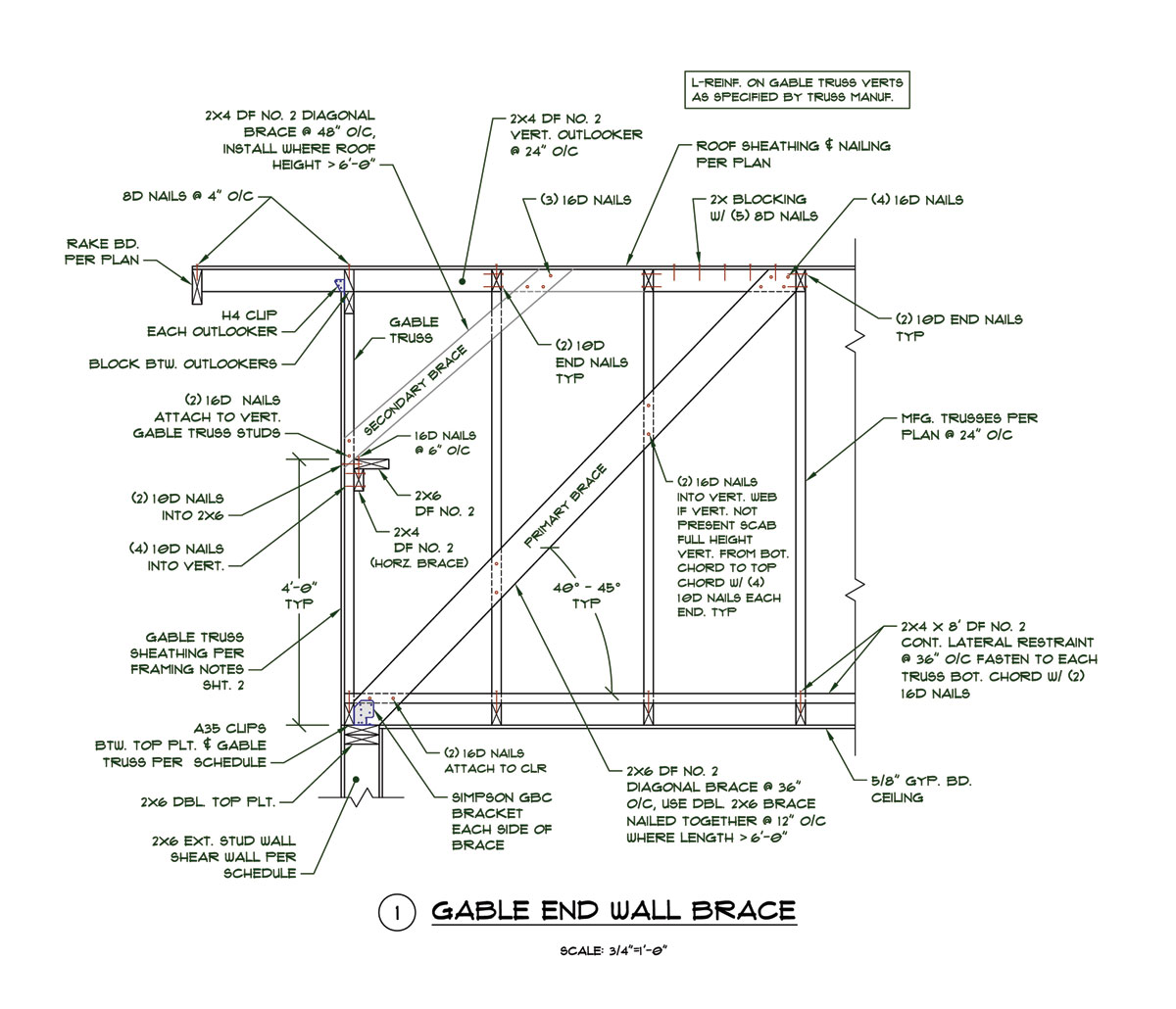
I like to use H4 clips on the outlookers, since they are small enough for application to either vert. or horiz. outlookers. However, at lateral load capacity of 165 lbs each it would be hard to rely on just these clips for any significant shear wall loads. The 2x solid blocking will either need additional toe-nailing, sheathing or LTP4 connectors to allow for more shear transfer.
Rather than use a dropped top chord truss I think it would be easier to bump up the depth of the top chord member and then notch out for the outlookers as required. This solves the connection problem described above and would seem like a much stronger connection at this location.
What do you see with residential roofs in your neck of the woods? Are dropped top chord trusses with structural outlookers the norm and if they are how do you deal with them?
A confused student is a good student.
Nathaniel P. Wilkerson, PE