muksidin taslim
Chemical
Hello ...
In our plant, our compressor machine can not reach the design point pressure, our team has performed to evaluate it. The IGV opening, pressure & temperature suction seem normal as usually. But the difference conditions are the temperature after 1st stage, 2nd stage and 3rd stage relative more high than previous operation. In this case, whether if the temperature discharge on each after cooler relative more high, the discharge pressure can not reach?
See the picture at below for actual condition
In our plant, our compressor machine can not reach the design point pressure, our team has performed to evaluate it. The IGV opening, pressure & temperature suction seem normal as usually. But the difference conditions are the temperature after 1st stage, 2nd stage and 3rd stage relative more high than previous operation. In this case, whether if the temperature discharge on each after cooler relative more high, the discharge pressure can not reach?
See the picture at below for actual condition
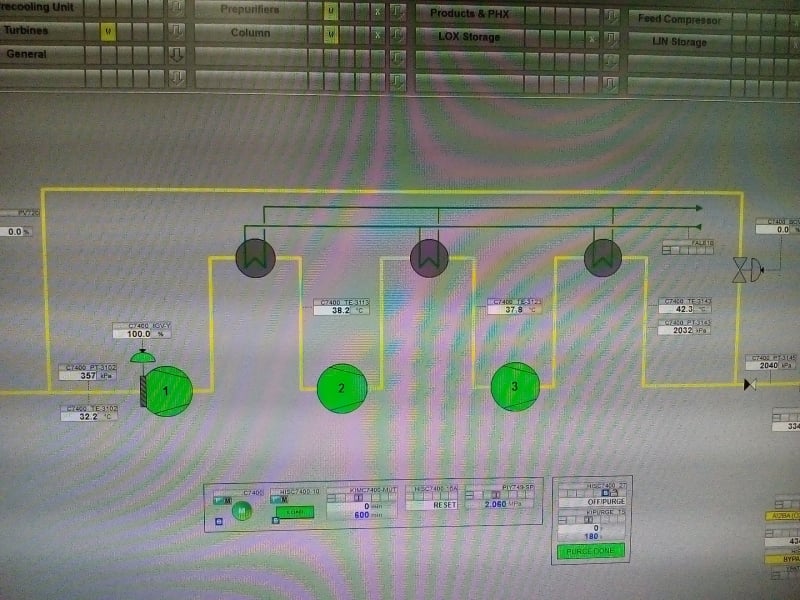