Gymnast
Electrical
- Mar 22, 2008
- 22
Before I even considered calculating, and for a small project I ordered two kind of steel rings from here:
Some 4 x 40 mm rings and 5 x 50 mm rings, and they have specified breaking strengths of 800 kgf and 1600 kgf.
I decided to make some simple pull testing of the rings, and found, that plastic deformation of the rings occurred at about 10% of the breaking strength. I was surprised by this low level, but I am no structural engineer. But after some simple structural calculations, it appears to me, that this can very well be the case. Actually the plastic deformation might occur at even lower load levels.
The specified breaking strengths from the supplier refer to a completely plastic distorted ring. If we assume two Ø5 steel wires with uniform stress, I can calculated the breaking stress to be 401 MPa.
A very simple calculation for the initial moment for plastic deformation of the thread would be M = 25 mm x F/2 where F is the force applied. Then no moment is applied from "the side". If we assume plastic deformation at 401 MPa then I get F= 394 N or 40 kgf. But I noticed the deformation starting at a force of about 160 kgf.
I have tried to look in Roark's formulas on curved beams, but I have a hard time selecting the right formula.
At what load level can you expect plastic deformation to start at such rings. Please help.
Some 4 x 40 mm rings and 5 x 50 mm rings, and they have specified breaking strengths of 800 kgf and 1600 kgf.
I decided to make some simple pull testing of the rings, and found, that plastic deformation of the rings occurred at about 10% of the breaking strength. I was surprised by this low level, but I am no structural engineer. But after some simple structural calculations, it appears to me, that this can very well be the case. Actually the plastic deformation might occur at even lower load levels.
The specified breaking strengths from the supplier refer to a completely plastic distorted ring. If we assume two Ø5 steel wires with uniform stress, I can calculated the breaking stress to be 401 MPa.
A very simple calculation for the initial moment for plastic deformation of the thread would be M = 25 mm x F/2 where F is the force applied. Then no moment is applied from "the side". If we assume plastic deformation at 401 MPa then I get F= 394 N or 40 kgf. But I noticed the deformation starting at a force of about 160 kgf.
I have tried to look in Roark's formulas on curved beams, but I have a hard time selecting the right formula.
At what load level can you expect plastic deformation to start at such rings. Please help.
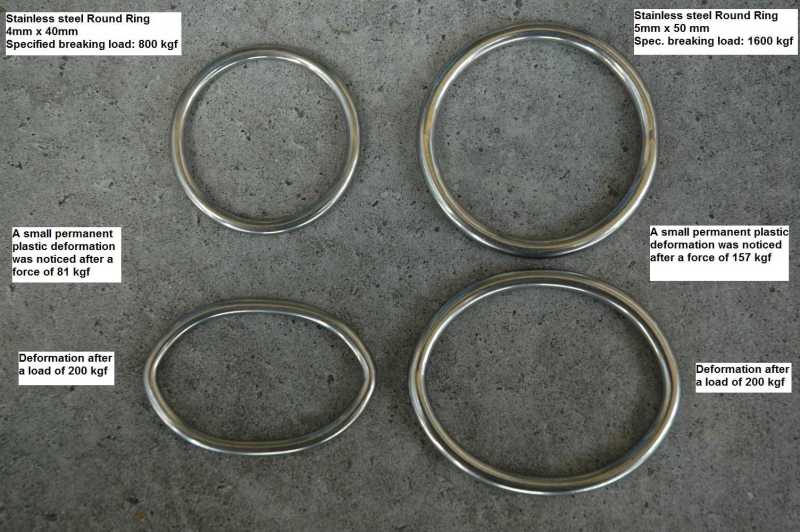