Mr_Curious
Mechanical
- Jul 14, 2020
- 47
Hello everyone.
I am looking for a static coefficient of friction between two milled dry A 516-55 steel surfaces for calculating a threaded connection. I have found a table of friction coefficients in Nasa's Fasteners design manual (below). There two types of steel I can choose from. Which is hard and mild. And in my opinion, coefficients are too big (0.74 and 0.78). Also, I am not sure if it is about milled surfaces.
Could anyone tell me whether one of those coefficients is right for my case or not? And provide me with a source, please.
I am looking for a static coefficient of friction between two milled dry A 516-55 steel surfaces for calculating a threaded connection. I have found a table of friction coefficients in Nasa's Fasteners design manual (below). There two types of steel I can choose from. Which is hard and mild. And in my opinion, coefficients are too big (0.74 and 0.78). Also, I am not sure if it is about milled surfaces.
Could anyone tell me whether one of those coefficients is right for my case or not? And provide me with a source, please.
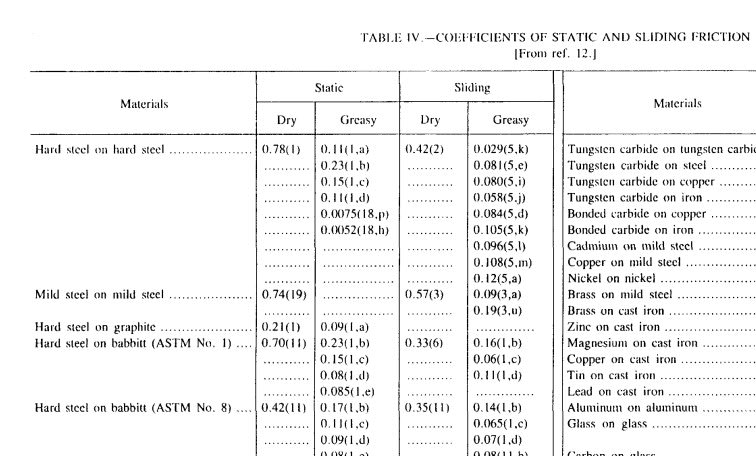