bnickeson
Structural
- Apr 7, 2009
- 81
The energy conservation code has - apparently for some time now - had a requirement for insulation at the perimeter of a concrete slab-on-grade. This requirement is pictured below.
The key language in there is "The insulation shall extend downward from the top of the slab". Up until recently, virtually everyone in our area of the country had either not known about this requirement or had ignored it. Building officials didn't seem to know about it either because no one had ever commented on drawings about it until relatively recently. Now a few of them have started taking notice. Basically this requirement is specifying that the perimeter of your slab-on-grade has to have 2" of insulation between it and your exterior wall. Your exterior wall could be masonry, concrete, a small concrete stem wall under a light gauge exterior wall (as is most common in commercial projects around here), etc. Aside from this requirement being utterly ridiculous, it presents some very annoying detailing and construction challenges. I've pictured three typical construction details below...assume that the exterior grade is level with the slab. The left one is our classical way of detailing a perimeter wall, the center one uses the 2" of insulation between the slab and perimeter wall, and the right one tapers the insulation and slab to a tip which is apparently permitted. The two "code-compliant" details on the right are a pain for obvious reasons. They're unsightly if you have exposed concrete floors, the tapered tip of the slab is likely to chip away over time, they don't offer a sealed joint to accommodate slab shrinkage, door thresholds at exterior openings are a nightmare, and architects tell me they're not supposed to leave this insulation exposed due to fire reasons.
So I'm asking a) Is everyone else here detailing their perimeter edges according to this code provision; and b) if you are, how are you detailing it? Over the last couple of years neither us nor our architectural clients have figured out a good way of detailing this without something being a problem. And since this detail is incredibly pointless even from an energy conservation perspective, I'm at my wits end with it and am looking for suggestions. Thanks in advance.

The key language in there is "The insulation shall extend downward from the top of the slab". Up until recently, virtually everyone in our area of the country had either not known about this requirement or had ignored it. Building officials didn't seem to know about it either because no one had ever commented on drawings about it until relatively recently. Now a few of them have started taking notice. Basically this requirement is specifying that the perimeter of your slab-on-grade has to have 2" of insulation between it and your exterior wall. Your exterior wall could be masonry, concrete, a small concrete stem wall under a light gauge exterior wall (as is most common in commercial projects around here), etc. Aside from this requirement being utterly ridiculous, it presents some very annoying detailing and construction challenges. I've pictured three typical construction details below...assume that the exterior grade is level with the slab. The left one is our classical way of detailing a perimeter wall, the center one uses the 2" of insulation between the slab and perimeter wall, and the right one tapers the insulation and slab to a tip which is apparently permitted. The two "code-compliant" details on the right are a pain for obvious reasons. They're unsightly if you have exposed concrete floors, the tapered tip of the slab is likely to chip away over time, they don't offer a sealed joint to accommodate slab shrinkage, door thresholds at exterior openings are a nightmare, and architects tell me they're not supposed to leave this insulation exposed due to fire reasons.
So I'm asking a) Is everyone else here detailing their perimeter edges according to this code provision; and b) if you are, how are you detailing it? Over the last couple of years neither us nor our architectural clients have figured out a good way of detailing this without something being a problem. And since this detail is incredibly pointless even from an energy conservation perspective, I'm at my wits end with it and am looking for suggestions. Thanks in advance.
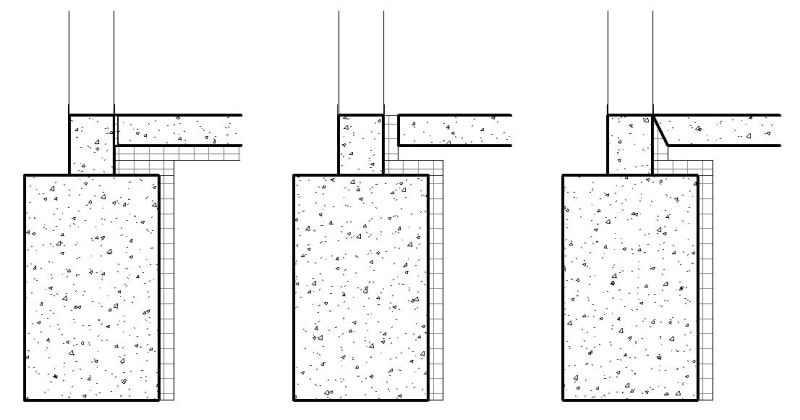