Hi there,
We are building some CFRP boxes with a metal mould. We are using aluminium G.AL® C330 (EN AW 7021 [AlZn5,5Mg1,5] from Gleich Germany) and Prepreg SIGRAPREG® C W205-TW2/2-E323/43%
We cured 3 hours at 120ºC (248F).
The unmoulding wasn't easy. It got stack on the inner walls of the mould.
We used 3 layers of Loctite Frekote 770NC. In the past we used it on a stainles steel mould with a E022 resin without problems
Attached some pictures
What do you think the problem could be? Maybe it was cured too long?
thanks
regards,
We are building some CFRP boxes with a metal mould. We are using aluminium G.AL® C330 (EN AW 7021 [AlZn5,5Mg1,5] from Gleich Germany) and Prepreg SIGRAPREG® C W205-TW2/2-E323/43%
We cured 3 hours at 120ºC (248F).
The unmoulding wasn't easy. It got stack on the inner walls of the mould.
We used 3 layers of Loctite Frekote 770NC. In the past we used it on a stainles steel mould with a E022 resin without problems
Attached some pictures
What do you think the problem could be? Maybe it was cured too long?
thanks
regards,
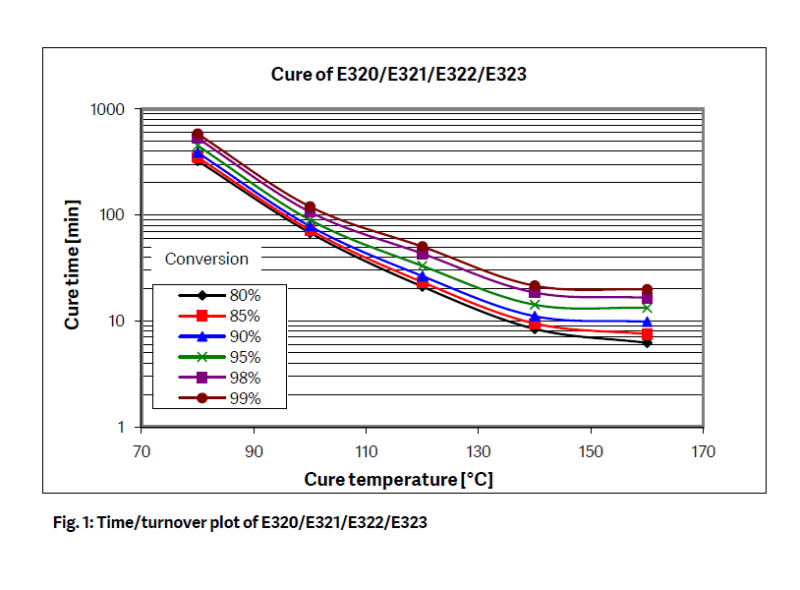
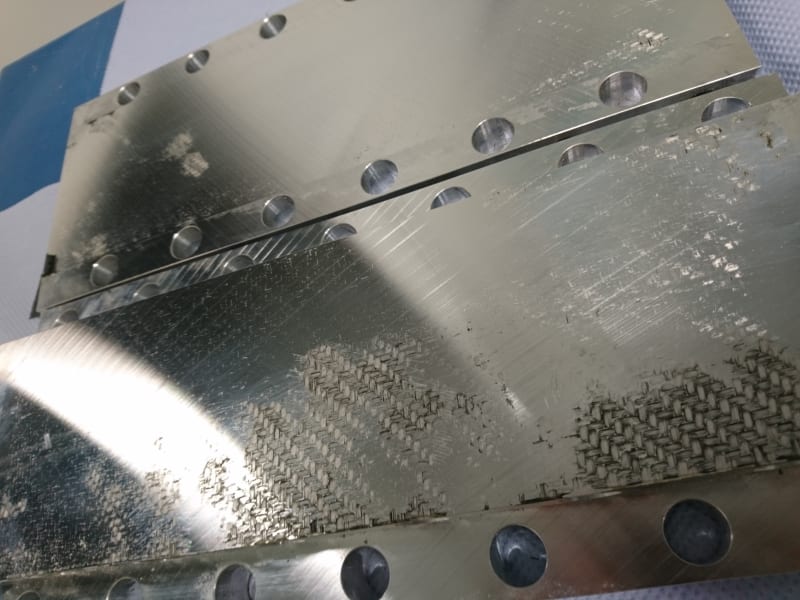
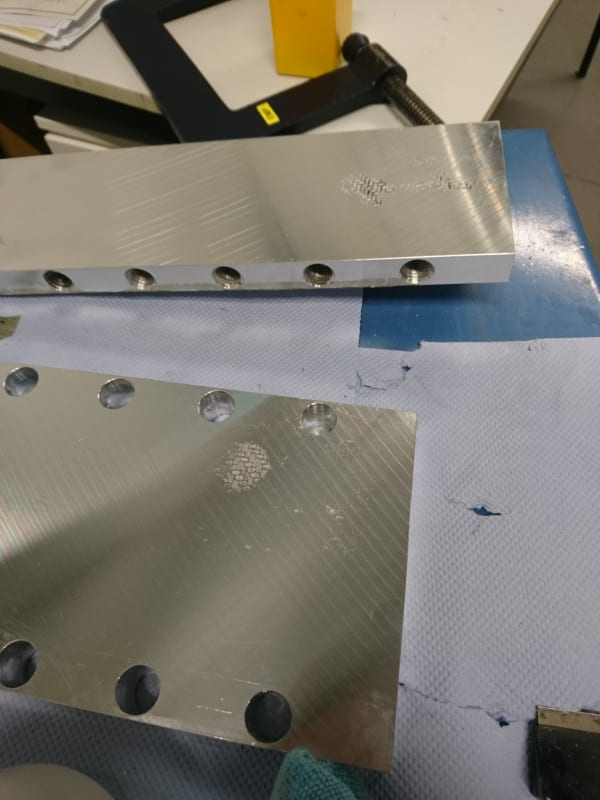