tmoe
Civil/Environmental
- Mar 3, 2011
- 33
See attached photo for reference.
Basically, this W10x12 outrigger had its bottom flange removed for aesthetic purposes without coordination of the structural team.
While the original beam was well designed for conservative eave snow loads, particularly heavy cornices have developed at the eaves, and in combination with the altered beam section, the web is buckling near the support.
Looking for recommendations on a field repair for the damaged beam.
I was hypothesizing that perhaps heat treatment to form the web back to vertical and then add welded side plates to strengthen the section.
I'm unclear on the pitfalls of heat treatment on a yielding member though.
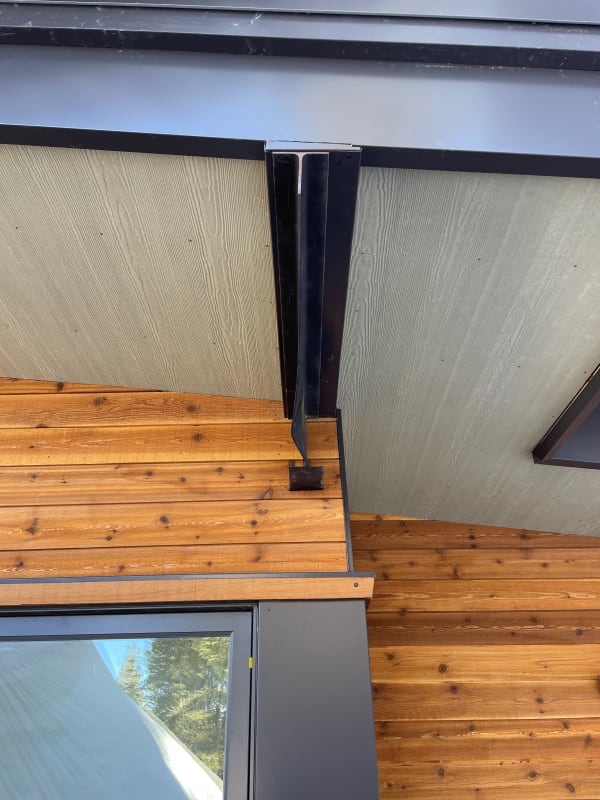
Basically, this W10x12 outrigger had its bottom flange removed for aesthetic purposes without coordination of the structural team.
While the original beam was well designed for conservative eave snow loads, particularly heavy cornices have developed at the eaves, and in combination with the altered beam section, the web is buckling near the support.
Looking for recommendations on a field repair for the damaged beam.
I was hypothesizing that perhaps heat treatment to form the web back to vertical and then add welded side plates to strengthen the section.
I'm unclear on the pitfalls of heat treatment on a yielding member though.