tuggernuts
Agricultural
I am not an engineer at all.
Question: I was thinking of building a tensioning mechanism for rolling out fencing wire/cable from the back of a moving vehicle, as it goes down the fenceline. The mechanism for tensioning the wire is by using an upright rotating steel pillar around which the wire is wrapped a couple of times before it is strained out, to prevent slippage. Attached to the bottom of this pillar is a spur gear of diameter 40cm with thick heavy teeth, which (being bolted flat to the to the bottom of the pillar) rotates as the pillar turns. This spur gear comes into contact, one tooth at a time, with a parallel single locking tooth, which pushes hard against the rotating cog. A certain amount of force is needed for this locking tooth to be pushed past. This parallel tooth is essentially a big lever, with the end furthest from the spur gear being tensioned by a spring in order to be able to push against the direction of motion of the spur gear. The fulcrum of this lever is about 100mm away from the rotating cog, and the spring tensioned end is about 1500mm away from the fulcrum (to reduce the force needed by the tensioning spring). The amount of tension on this tooth would be significant, up to a max of around 1.6 tonnes. My question is, would this be feasible in terms of longevity of the locking tooth and the spur gear? how long would each last if, say the rotating cylinder to which the spur gear is attached to rotates around 5000 times per day? would a seriously heavy duty gear and tooth be needed to be able to withstand such an amount of force?
Cheers
Question: I was thinking of building a tensioning mechanism for rolling out fencing wire/cable from the back of a moving vehicle, as it goes down the fenceline. The mechanism for tensioning the wire is by using an upright rotating steel pillar around which the wire is wrapped a couple of times before it is strained out, to prevent slippage. Attached to the bottom of this pillar is a spur gear of diameter 40cm with thick heavy teeth, which (being bolted flat to the to the bottom of the pillar) rotates as the pillar turns. This spur gear comes into contact, one tooth at a time, with a parallel single locking tooth, which pushes hard against the rotating cog. A certain amount of force is needed for this locking tooth to be pushed past. This parallel tooth is essentially a big lever, with the end furthest from the spur gear being tensioned by a spring in order to be able to push against the direction of motion of the spur gear. The fulcrum of this lever is about 100mm away from the rotating cog, and the spring tensioned end is about 1500mm away from the fulcrum (to reduce the force needed by the tensioning spring). The amount of tension on this tooth would be significant, up to a max of around 1.6 tonnes. My question is, would this be feasible in terms of longevity of the locking tooth and the spur gear? how long would each last if, say the rotating cylinder to which the spur gear is attached to rotates around 5000 times per day? would a seriously heavy duty gear and tooth be needed to be able to withstand such an amount of force?
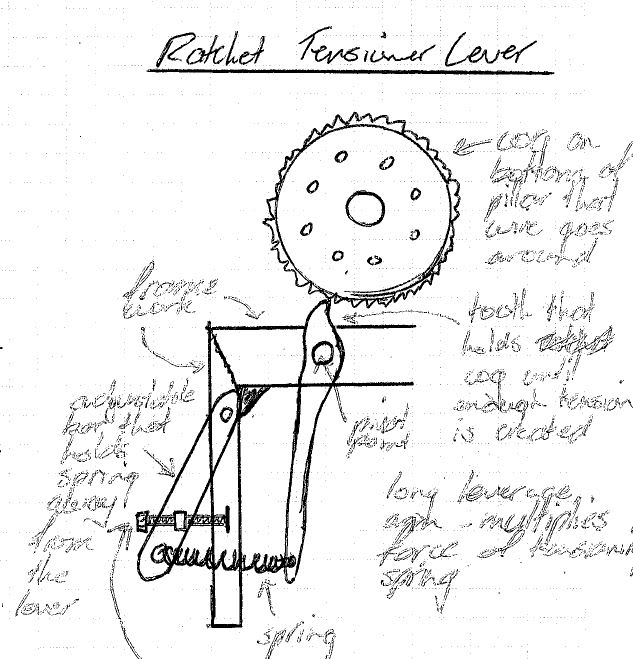
Cheers