Jalbno
Structural
- Nov 11, 2020
- 6
Good day to all,
I have this weld that I am trying to analyze. I understand that it may be somewhat ugly and inefficient, but I am in a position in which I still need to calculate this.
The only reason I am considering this spec is because the load on the end of this beam is very very small.
The loaded cantilevered member is a rectangular HSS, welded to the top of this other steel member. I'm worried about the moment resistance of this weld, would I calculate it it using the section modulus of the weld multiplied by the strength of the weld material about the axis of rotation?
Thanks for you time.
NJ
I have this weld that I am trying to analyze. I understand that it may be somewhat ugly and inefficient, but I am in a position in which I still need to calculate this.
The only reason I am considering this spec is because the load on the end of this beam is very very small.
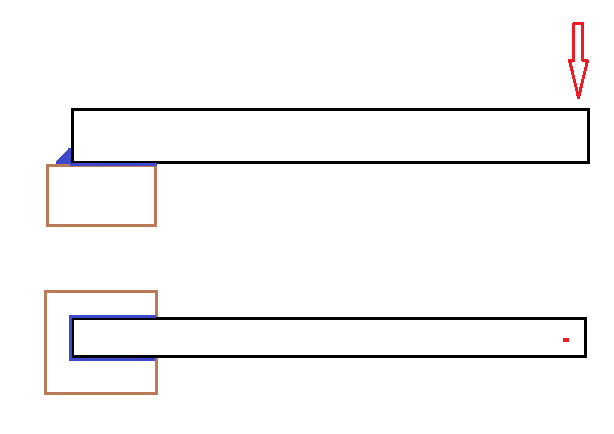
The loaded cantilevered member is a rectangular HSS, welded to the top of this other steel member. I'm worried about the moment resistance of this weld, would I calculate it it using the section modulus of the weld multiplied by the strength of the weld material about the axis of rotation?
Thanks for you time.
NJ