KootK
Structural
- Oct 16, 2001
- 18,611
My favorite precaster has some strand that has become permanently kinked in the unloaded state. Their speculative explanation for the cause is that the strand has been pulled off of the spool and through the pulling head at too sharp of an angle. The questions that we're trying to answer are these:
1) Are there additional explanations that should be considered?
2) What are the limits of acceptability on this? Does this section of strand need to be scrapped or can it be pulled taught and used?
I don't know the answer to this which is why I've created this thread and have reached out to PCI. I do have the following thoughts, however:
3) Even with some locked in, inelastic plastic stresses, I suspect that the strand could probably just "pull through" to the normally assumed, full tension stress state given that the locked in bending is internally self-equilibrating.
4) I know that prestressing strand is less ductile than say, mild rebar, and does need to be babied a bit more to prevent fracture. I worry somewhat that, even with the pull through mechanism of #3, the individual wires of the strand may be at substantially different tensile strains when that uniform stress is reached and that may result in premature tensile fracture of some strands.
5) I worry a bit that the winding of the strands may have come apart somewhat during the bending process such that, when they come back together, perhaps there will be detrimental stress concentrations etc.
6) When prestressing strand is intentionally deviated / harped, the curvature induced in the strand would typically be considerably more than the photo shows. That’s encouraging although the difference may be the more controlled environment under which the deviation is applied.
So what do we think, can strand bent like this still be used?
1) Are there additional explanations that should be considered?
2) What are the limits of acceptability on this? Does this section of strand need to be scrapped or can it be pulled taught and used?
I don't know the answer to this which is why I've created this thread and have reached out to PCI. I do have the following thoughts, however:
3) Even with some locked in, inelastic plastic stresses, I suspect that the strand could probably just "pull through" to the normally assumed, full tension stress state given that the locked in bending is internally self-equilibrating.
4) I know that prestressing strand is less ductile than say, mild rebar, and does need to be babied a bit more to prevent fracture. I worry somewhat that, even with the pull through mechanism of #3, the individual wires of the strand may be at substantially different tensile strains when that uniform stress is reached and that may result in premature tensile fracture of some strands.
5) I worry a bit that the winding of the strands may have come apart somewhat during the bending process such that, when they come back together, perhaps there will be detrimental stress concentrations etc.
6) When prestressing strand is intentionally deviated / harped, the curvature induced in the strand would typically be considerably more than the photo shows. That’s encouraging although the difference may be the more controlled environment under which the deviation is applied.
So what do we think, can strand bent like this still be used?
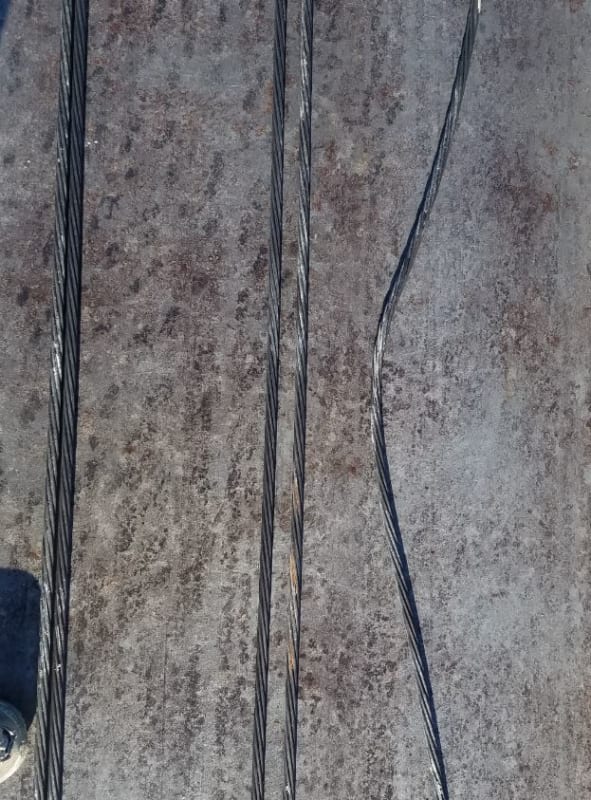