Jimbob218
Mechanical
- Jun 1, 2016
- 2
Hello all,
I am done with the 1st half of my BSME so I have touched on this type of thing but as for the actual application I am having trouble. I am trying to design a bracket to hold a small (110 lb) outboard motor on the back of my boat. Right now I have it modeled with .125'' thk 6061-T6 mostly because we have a large sheet of it at my work I can use for free, but I want to make sure it will hold up. I want to figure out what forces will be acting on the bracket as the motor bounces around while going over waves or while on the trailer.
Thanks in advance for your help!
I am done with the 1st half of my BSME so I have touched on this type of thing but as for the actual application I am having trouble. I am trying to design a bracket to hold a small (110 lb) outboard motor on the back of my boat. Right now I have it modeled with .125'' thk 6061-T6 mostly because we have a large sheet of it at my work I can use for free, but I want to make sure it will hold up. I want to figure out what forces will be acting on the bracket as the motor bounces around while going over waves or while on the trailer.
Thanks in advance for your help!
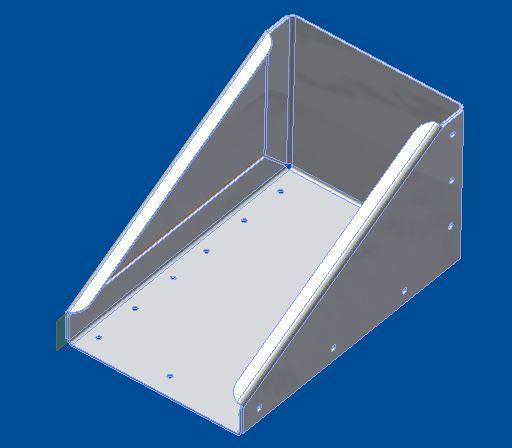