SteelPE
Structural
- Mar 9, 2006
- 2,759
Maybe this isn't a good question to ask because I know absolutely nothing about the project, but I received a question from a fabricator client recently and I am wondering the answer myself. Attached you will find a picture of some painted HSS columns. The column has a hole drilled in the base of the column. He said that all of the columns have this hole at the base.
I know you would typically provide a hole for vending during galvanizing, however, these columns appear to be painted. I was wondering if it was for drainage during erection. I am now wondering if I am suppose to be providing holes in the bottom of my HSS columns (not really).
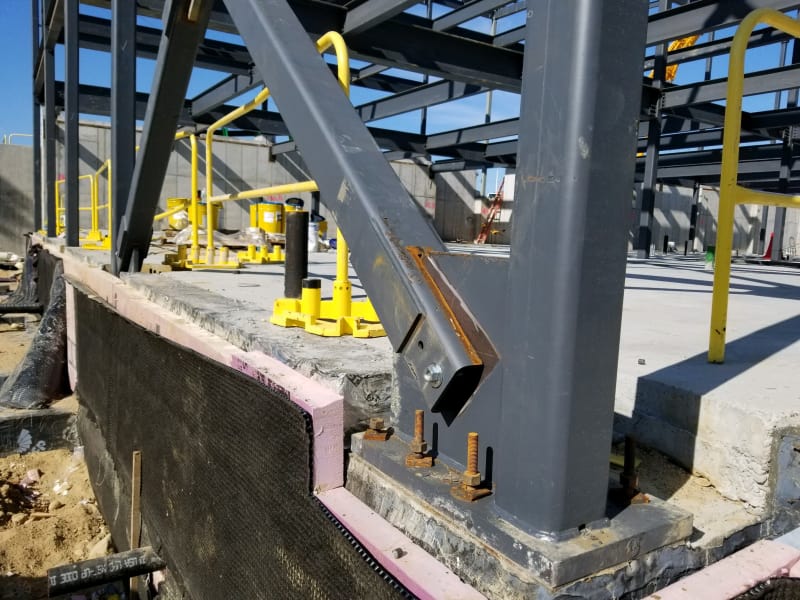
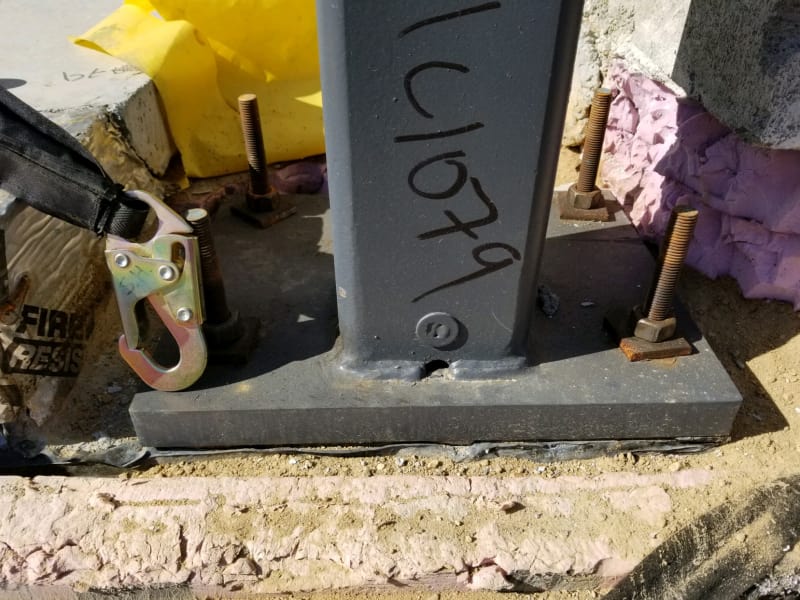
I know you would typically provide a hole for vending during galvanizing, however, these columns appear to be painted. I was wondering if it was for drainage during erection. I am now wondering if I am suppose to be providing holes in the bottom of my HSS columns (not really).