Hello, everyone.
I will be performing stress relief heat treatment on 4140 steel specifically for a part as shown in the image with these measurements.
My question is, what thickness is appropriate for heating, since the standard tells me that it should be at least 1 hour per inch?
And generally, what heating ramp do you use?
Thank you for your support.
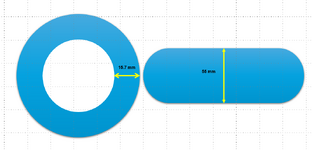
I will be performing stress relief heat treatment on 4140 steel specifically for a part as shown in the image with these measurements.
My question is, what thickness is appropriate for heating, since the standard tells me that it should be at least 1 hour per inch?
And generally, what heating ramp do you use?
Thank you for your support.
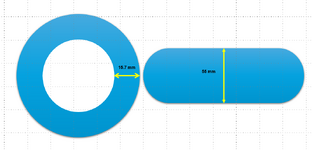