Hello everyone,
Could you help me out from a finite element simulation problem? I have some questions on finite element simulation of a single Twaron yarn under tensile loading to failure situation using Abaqus. The results are compared to the tension tests on such a yarn:
[ul]
[li]yarn length is 250 mm;[/li]
[li]pulling speed is 1.66667 mm/s;[/li]
[li]the failure strength is about 2.6 GPa while load at break is about 170 N;[/li]
[li]and the elongation at broken is about 4%.[/li]
[/ul]
The yarn consists of hundreds of Twaron fibres in a parallel way. The fibre can be treated as isotropic material but the yarn has been assigned mechanical properties according to a transversely isotropic material model in the FEA. Such consideration can be found in the paper of Y Duan's work [Finite element modeling of transverse impact on a ballistic fabric].
I am trying to simulate the behaviour of the yarn under tensile loading along the longitudinal direction to get the stress-strain curve including the segment of failure. If I apply the material properties and failure criteria, which is assuming to be ductile damage, on a single element model, I can get reasonable results. But if I use a realistic model, the results are so different. What I have tried is explained as follows.
In my model,
[ul]
[li]density is 1.44e3 kg/m^3;[/li]
[li]the yarn is modelled as a homogenised rod with a cross-sectional area of 0.0946 mm^2;[/li]
[li]the engineering constants are 77e9, 0.77e9, 0.77e9, 0, 0, 0, 0.3869e9, 0.3869e9, 0.3869e9, which are E1, E2, E3, v12, v13, v23, G12, G13, G23 respectively;[/li]
[li]plasticity is isotropic with 2.6GPa, 0 in the table and only this one line;[/li]
[li]damage is ductile with 0.00355, 1, 0 as the fracture strain, stress triaxiality and strain rate, and the evolution energy is set to be 600J/m^2.[/li]
[/ul]
I just want to know what I am doing wrong about these.
1. FEA on a 1cm long yarn using explicit (dynamic) method.
2. FEA on a 250mm model which is separated into standard (static) method and explicit method.
Any comments are appreciated.
Thanks in advance.
Regards,
cnzhx
Could you help me out from a finite element simulation problem? I have some questions on finite element simulation of a single Twaron yarn under tensile loading to failure situation using Abaqus. The results are compared to the tension tests on such a yarn:
[ul]
[li]yarn length is 250 mm;[/li]
[li]pulling speed is 1.66667 mm/s;[/li]
[li]the failure strength is about 2.6 GPa while load at break is about 170 N;[/li]
[li]and the elongation at broken is about 4%.[/li]
[/ul]
The yarn consists of hundreds of Twaron fibres in a parallel way. The fibre can be treated as isotropic material but the yarn has been assigned mechanical properties according to a transversely isotropic material model in the FEA. Such consideration can be found in the paper of Y Duan's work [Finite element modeling of transverse impact on a ballistic fabric].
I am trying to simulate the behaviour of the yarn under tensile loading along the longitudinal direction to get the stress-strain curve including the segment of failure. If I apply the material properties and failure criteria, which is assuming to be ductile damage, on a single element model, I can get reasonable results. But if I use a realistic model, the results are so different. What I have tried is explained as follows.
In my model,
[ul]
[li]density is 1.44e3 kg/m^3;[/li]
[li]the yarn is modelled as a homogenised rod with a cross-sectional area of 0.0946 mm^2;[/li]
[li]the engineering constants are 77e9, 0.77e9, 0.77e9, 0, 0, 0, 0.3869e9, 0.3869e9, 0.3869e9, which are E1, E2, E3, v12, v13, v23, G12, G13, G23 respectively;[/li]
[li]plasticity is isotropic with 2.6GPa, 0 in the table and only this one line;[/li]
[li]damage is ductile with 0.00355, 1, 0 as the fracture strain, stress triaxiality and strain rate, and the evolution energy is set to be 600J/m^2.[/li]
[/ul]
I just want to know what I am doing wrong about these.
1. FEA on a 1cm long yarn using explicit (dynamic) method.
I tried to keep a same pulling speed as that in the experiments, which is set to be a displacement of 0.5 mm on one end in 0.3s.
But the load at break is about 40 N. (Sorry that I am re-running the simulation and could not get a graph on the load-displacement curve.
But the load at break is about 40 N. (Sorry that I am re-running the simulation and could not get a graph on the load-displacement curve.
2. FEA on a 250mm model which is separated into standard (static) method and explicit method.
The STANDARD (static) part is good, but the explicit (dynamic) part is not.
[ul]
[li]The yarn shows a undulation after switching to Dynamic/Explicit method, attached fig 1
[/li]
[li]The Load - Displacement/Original Length curve is not right compared to the experiment curve, attached fig 2
[/li]
[/ul]
[ul]
[li]The yarn shows a undulation after switching to Dynamic/Explicit method, attached fig 1
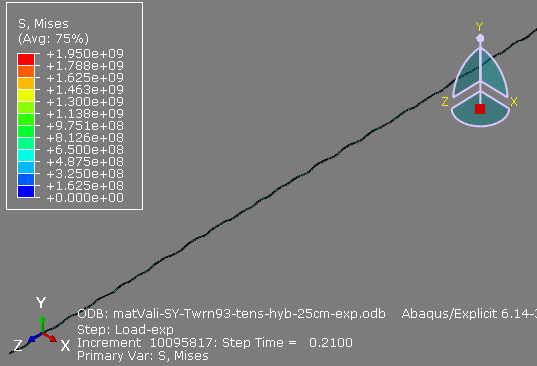
[/li]
[li]The Load - Displacement/Original Length curve is not right compared to the experiment curve, attached fig 2
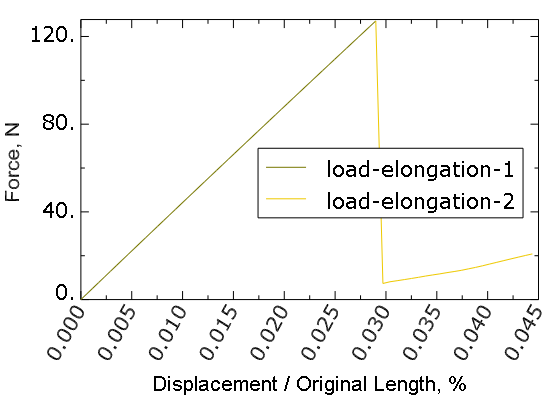
[/li]
[/ul]
Any comments are appreciated.
Thanks in advance.
Regards,
cnzhx