Samwise Gamgee
Structural
- Oct 7, 2021
- 118
I am trying to resolve forces in the braced frames on roof. Unfortunately the deck does not have enough capacity to transfer shear over the braced frames, so I have to rely on beams in other bays to act as collector elements. However the beams are not in the same straight line to transfer the load into the braced frames due to stairs in the middle. How do I provide a continuous load path from Beam-2 to Beam-3 and from Beam -3 to Beam-4 ? (Attached a screenshot)
The only other solution is to place side lap fasteners as close as 3" to increase the shear capacity and drag all of that load in the braced frames. But this is very expensive.
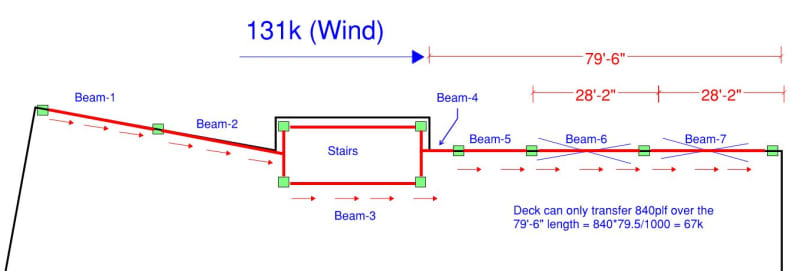
The only other solution is to place side lap fasteners as close as 3" to increase the shear capacity and drag all of that load in the braced frames. But this is very expensive.