pyromech
Mechanical
- Jul 30, 2008
- 39
Folks
I always had trouble interpreting a cut vs protrusion. In Figure 1, the step feature has a dimension 0.296 -0.005". Wouldn't this cut read 0.296+0.005". The same for Figure 2. It boils down how is machined. Does anyone have a references to read? any tips.
I always had trouble interpreting a cut vs protrusion. In Figure 1, the step feature has a dimension 0.296 -0.005". Wouldn't this cut read 0.296+0.005". The same for Figure 2. It boils down how is machined. Does anyone have a references to read? any tips.
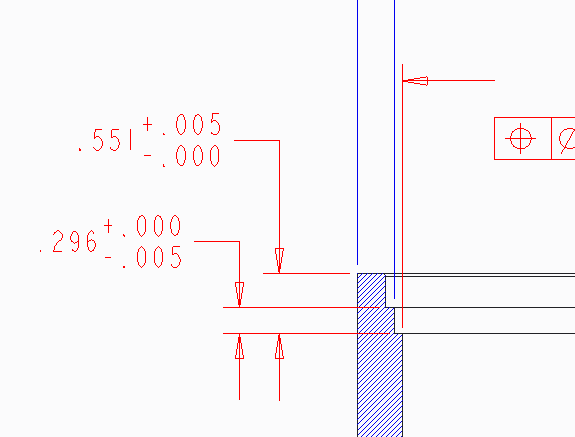