mferg318
Structural
- Oct 26, 2017
- 16
How is everyone handling transfer forces from discontinuous shear walls above a diaphragm, similar to the situation shown below? I'm specifically looking for how to incorporate the shear wall loads into the shear diagram for the diaphragm. Are you adding them as point loads, or distributing across the width of the diaphragm? There seems to be mixed opinions in the literature.
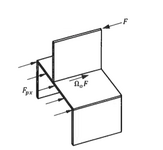
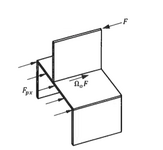