I have modeled a simple system of single pipe. The upstream is connected to a water reservoir RL(m)=80 & pipe RL(m)=20, Dia(m)=0.6 & Length(m)=5500. The downstream (end connection) is a shut-off valve discharging to atmosphere @ 0.12m^3/s. This valve is simulated to close at 0.01s abruptly
Now I have x2 graphs from which I need to comprehend:
1] Wave reflection time 2L/c ...more about this parameter: 2] System deceleration value
Now please audit if my comprehension is correct
From the 1st plot 2L/c = ~19.5s
so c = (2*5500)/19.5 = 564m/s
From 2nd plot system deceleration is
0.12/(0.25*pi*0.6^2) = 0.424m/s
0.424/2.5 = 0.17m/s^2
Now I have x2 graphs from which I need to comprehend:
1] Wave reflection time 2L/c ...more about this parameter: 2] System deceleration value
Now please audit if my comprehension is correct
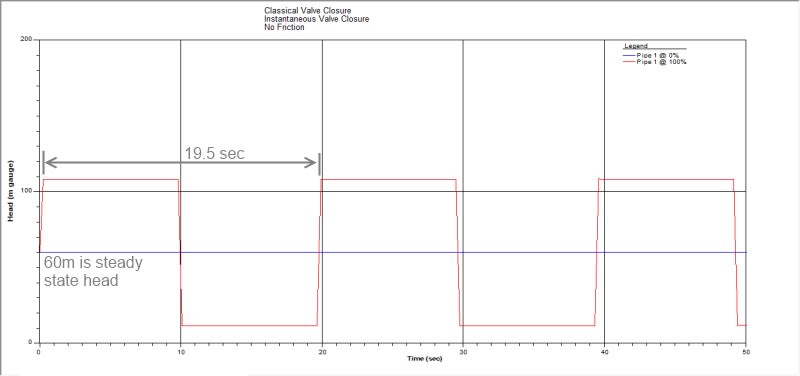
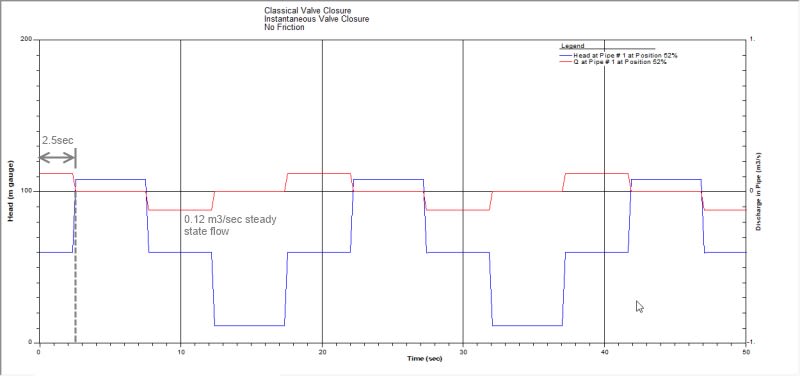
From the 1st plot 2L/c = ~19.5s
so c = (2*5500)/19.5 = 564m/s
From 2nd plot system deceleration is
0.12/(0.25*pi*0.6^2) = 0.424m/s
0.424/2.5 = 0.17m/s^2