jimmyhutmacher
Mechanical
- Jan 11, 2011
- 50
Hello All,
Any help or guidance on the following is greatly appreciated! I'm tasked with analyzing a built-up I-shaped member composed of A-992 WT7x11 and 304 SS 3/16" plate, under simply supported combined major axis bending and axial compression. I've done some research and believe using the transformed section (A.K.A. transformed width) method to find the moments/stresses followed by AISC 360-16 F4. OTHER I-SHAPED MEMBERS WITH COMPACT OR NONCOMPACT WEBS BENT ABOUT THEIR MAJOR AXIS to find the allowable moment is the way to go. However, what I'm getting hung up on is the requirement that the entire section must remain within the proportional limit (i.e., no part of the section can plastically yield) when using the transformed section method and from what I understand, AISC 360-16 F4 is based on some plastic yielding happening throughout the section. Is there a way to modify AISC 360-16 F4 to limit the yielding to the elastic limit or maybe there's another method that I should be using? Thanks in advance for your help!
Any help or guidance on the following is greatly appreciated! I'm tasked with analyzing a built-up I-shaped member composed of A-992 WT7x11 and 304 SS 3/16" plate, under simply supported combined major axis bending and axial compression. I've done some research and believe using the transformed section (A.K.A. transformed width) method to find the moments/stresses followed by AISC 360-16 F4. OTHER I-SHAPED MEMBERS WITH COMPACT OR NONCOMPACT WEBS BENT ABOUT THEIR MAJOR AXIS to find the allowable moment is the way to go. However, what I'm getting hung up on is the requirement that the entire section must remain within the proportional limit (i.e., no part of the section can plastically yield) when using the transformed section method and from what I understand, AISC 360-16 F4 is based on some plastic yielding happening throughout the section. Is there a way to modify AISC 360-16 F4 to limit the yielding to the elastic limit or maybe there's another method that I should be using? Thanks in advance for your help!
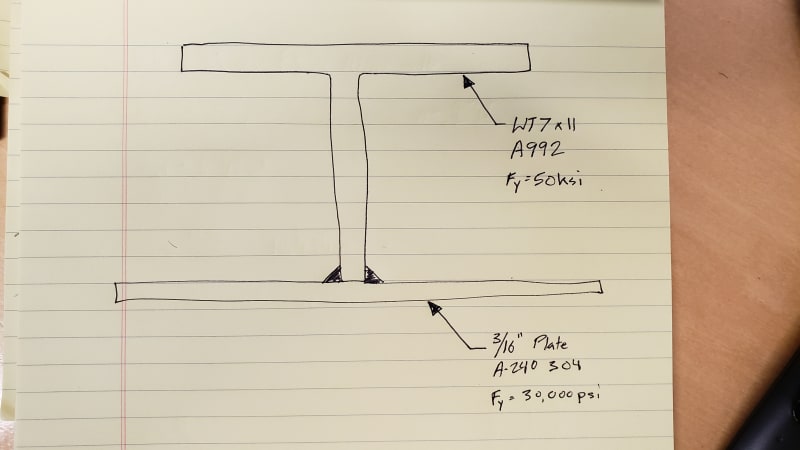