carson556
Student
- Mar 23, 2023
- 1
Hi everyone,
I'm using ABAQUS for linear buckling analysis of a circular tube under compression between 2 flat platens, however, I'm having trouble getting the same deformation mode as observed from several experimental literatures. I modelled the tube in axisymmetric elements with surface-to-surface contact between the top platen and the top surface of the tube, and bottom plate with the lower surface of the tube. The geometry and material I'm using comes from a paper. A tangent penalty friction of 0.05 & hard contact is applied between the plates and the tube surfaces. For the buckle step, a concentrated force of 1 in the U2 direction is applied on the reference point of the upper platen. According to the setup, the largest fold of the first eigenmode of the tube is observed to occur at the middle of the tube, in experiments, the buckling fold observed to happen at tube end in contact with the non-moving plate. Would the buckling mode shape from this analysis be the result of a wrong setup, or a lack of understanding between experimental and FEA results?
FEA setup:
Elastic properties
E=69.5GPa, v=0.33).
Geometry: (Outer tube radius=18mm, Tube thickness=2mm).
Mesh: 4 elements across tube thickness
BCs (Buckling step): Upper platen
U1=0; UR3=0); Lower platen
U1=U2=UR3=0)
Figures 1-3. (Left) Linear buckling analysis result. (Middle)Assembly view. (Right)Experimental results [Concertina deformation of tube]
I'm using ABAQUS for linear buckling analysis of a circular tube under compression between 2 flat platens, however, I'm having trouble getting the same deformation mode as observed from several experimental literatures. I modelled the tube in axisymmetric elements with surface-to-surface contact between the top platen and the top surface of the tube, and bottom plate with the lower surface of the tube. The geometry and material I'm using comes from a paper. A tangent penalty friction of 0.05 & hard contact is applied between the plates and the tube surfaces. For the buckle step, a concentrated force of 1 in the U2 direction is applied on the reference point of the upper platen. According to the setup, the largest fold of the first eigenmode of the tube is observed to occur at the middle of the tube, in experiments, the buckling fold observed to happen at tube end in contact with the non-moving plate. Would the buckling mode shape from this analysis be the result of a wrong setup, or a lack of understanding between experimental and FEA results?
FEA setup:
Elastic properties
Geometry: (Outer tube radius=18mm, Tube thickness=2mm).
Mesh: 4 elements across tube thickness
BCs (Buckling step): Upper platen
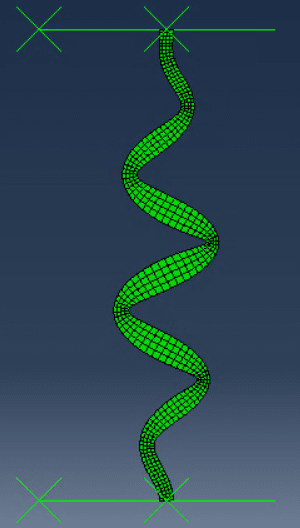
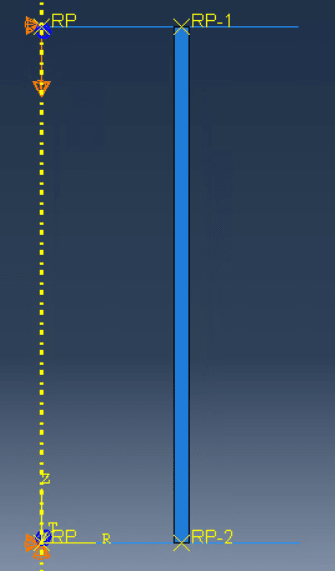
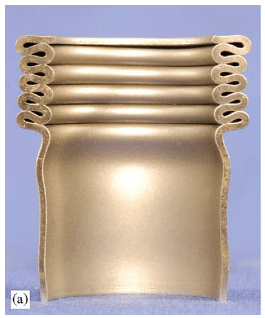
Figures 1-3. (Left) Linear buckling analysis result. (Middle)Assembly view. (Right)Experimental results [Concertina deformation of tube]