Euler07
Structural
- May 7, 2023
- 78
Hi everyone,
I have a cantilevered aluminium structure that needs a bolted moment connection between the column and rafter (see the image). The cantilever length is approx. 3m and the wall of the RHS is between 6mm to 9mm depending on the final design.
I was originally going with option 1, however the builder said the wall of the aluminium RHS sometimes deforms when tightening the bolts and asked if we need “crush tubes” (tubes inside the RHS that will prevent crushing of the RHS wall). I have searched for information on crush tubes in aluminium but can’t find anything. Does anyone have experience on this type of connection and was crushing of the wall an issue?
Otherwise, I was considering using option 2. However, the client doesn’t want gussets (they want a ‘clean’ look), therefore I would prefer option 1 where I can adjust the weld length on the column and bolt spacing on the rafter as required.
Any thoughts?
I have a cantilevered aluminium structure that needs a bolted moment connection between the column and rafter (see the image). The cantilever length is approx. 3m and the wall of the RHS is between 6mm to 9mm depending on the final design.
I was originally going with option 1, however the builder said the wall of the aluminium RHS sometimes deforms when tightening the bolts and asked if we need “crush tubes” (tubes inside the RHS that will prevent crushing of the RHS wall). I have searched for information on crush tubes in aluminium but can’t find anything. Does anyone have experience on this type of connection and was crushing of the wall an issue?
Otherwise, I was considering using option 2. However, the client doesn’t want gussets (they want a ‘clean’ look), therefore I would prefer option 1 where I can adjust the weld length on the column and bolt spacing on the rafter as required.
Any thoughts?
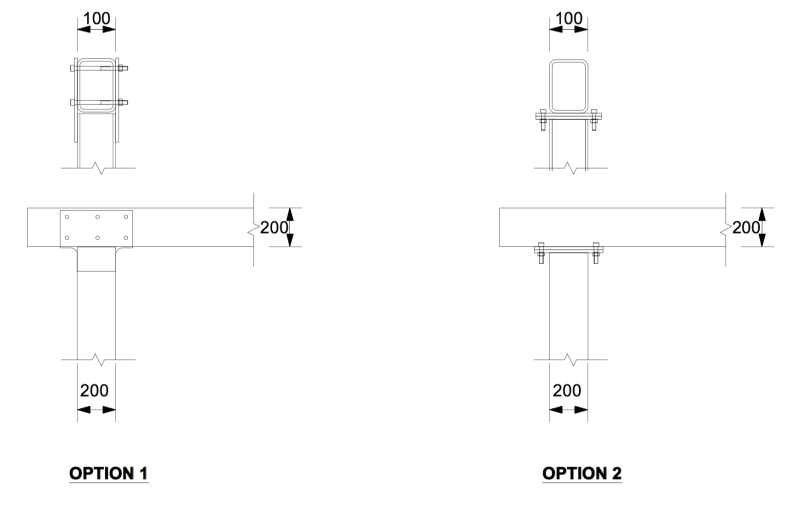