Hi,
I'm a newbie in the small electric motor hacking world.
I need info about how to drive a standard 120vac motor
with a variable AC source without overheating the motor
at low speed...
Here is my project:
Yamaha organ instrument used to include, in some of their organ,
what they called a rotary speaker unit which is in fact
a rotating speaker driven by a pulley and an 120VAC-60hz electric motor
driven by a variable speed circuit. (the 120VAC is lowered for slower speed)
Here attached are pictures of the unit, The motor driver circuit and
because I just have all the needed material to build
a clone of this unit BUT the special Yamaha AC motor,
I use a substitute motor for my project..
My problem is that my substitute motor which is the exact size/power
of the Yamaha is overheating when the VAC driving it is lowered.
I had to put a small fan over it to keep it from getting too hot !!
I suspect there is some windings in the Yamaha motor
that keeps the motor from overheating and accept
a lower AC than 120VAC..
Probably a current phase between stator and rotor
that gets 'upset' at slower speed than expected for 60hz use.. (??)
Can you tell what are the differences between both motors
and what type should I buy (and where) ??
Many Thanks !
Jean-Pierre Desrochers
Canada
I'm a newbie in the small electric motor hacking world.
I need info about how to drive a standard 120vac motor
with a variable AC source without overheating the motor
at low speed...
Here is my project:
Yamaha organ instrument used to include, in some of their organ,
what they called a rotary speaker unit which is in fact
a rotating speaker driven by a pulley and an 120VAC-60hz electric motor
driven by a variable speed circuit. (the 120VAC is lowered for slower speed)
Here attached are pictures of the unit, The motor driver circuit and
because I just have all the needed material to build
a clone of this unit BUT the special Yamaha AC motor,
I use a substitute motor for my project..
My problem is that my substitute motor which is the exact size/power
of the Yamaha is overheating when the VAC driving it is lowered.
I had to put a small fan over it to keep it from getting too hot !!
I suspect there is some windings in the Yamaha motor
that keeps the motor from overheating and accept
a lower AC than 120VAC..
Probably a current phase between stator and rotor
that gets 'upset' at slower speed than expected for 60hz use.. (??)
Can you tell what are the differences between both motors
and what type should I buy (and where) ??
Many Thanks !
Jean-Pierre Desrochers
Canada
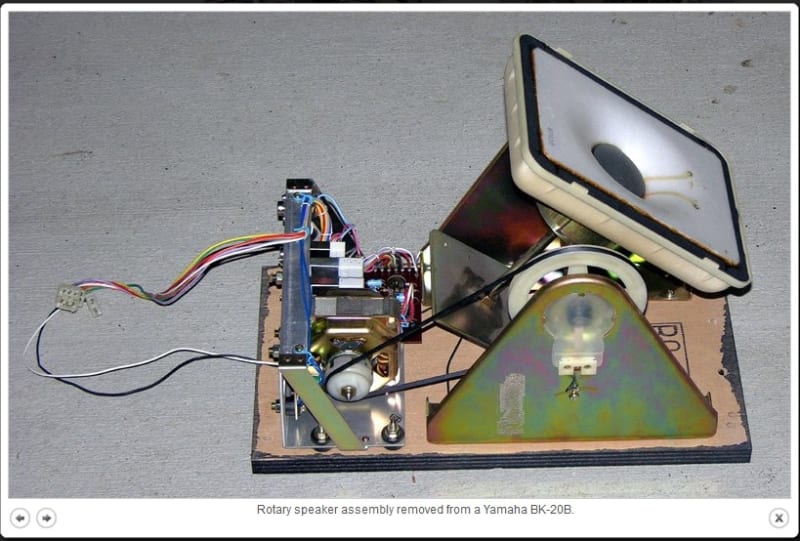
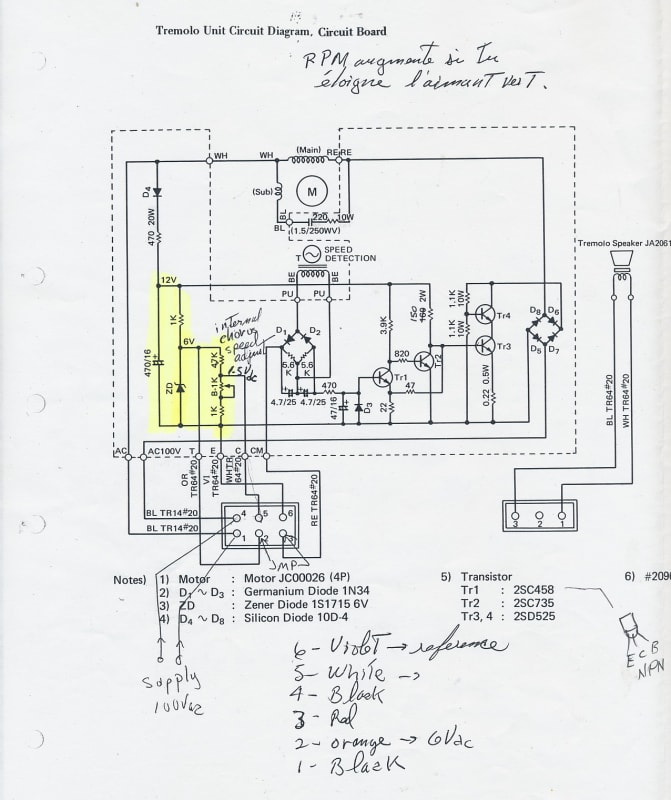
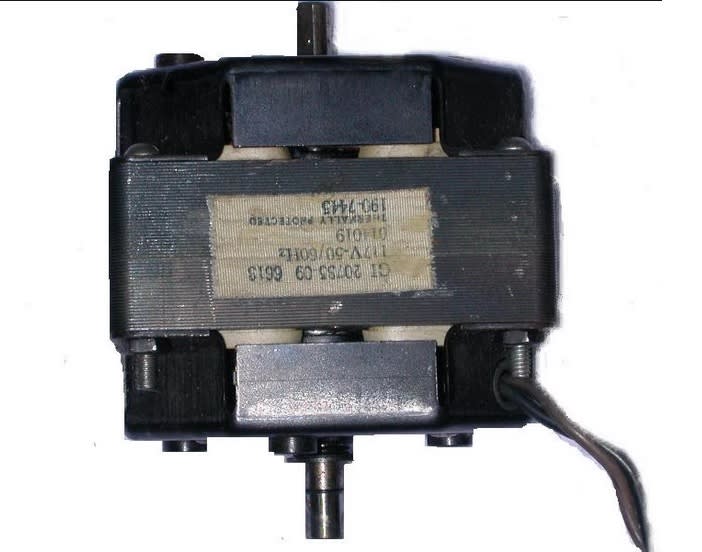