We have recently fabricated a 6-cavity hot runner injection mold for a 92mm HDPE plastic cap. The injection point is located at the center of the cap. We have conducted initial sampling, but we are experiencing an issue with the part.
Problem:
The cap is warping on the top surface after molding. The deformation appears to be consistent across all cavities and is affecting the flatness and overall quality of the cap.
Key Details:
What factors should we investigate first—material behavior, gate design, cooling layout, or processing parameters?
Any suggestions or advice would be greatly appreciated.
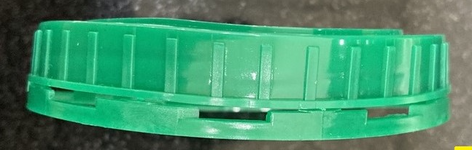
Problem:
The cap is warping on the top surface after molding. The deformation appears to be consistent across all cavities and is affecting the flatness and overall quality of the cap.
Key Details:
- Resin: HDPE
- Mold Type: 6 cavity hot runner
- Gate location: Center of the cap (direct injection)
- Warpage: On the top side of the cap
What factors should we investigate first—material behavior, gate design, cooling layout, or processing parameters?
Any suggestions or advice would be greatly appreciated.
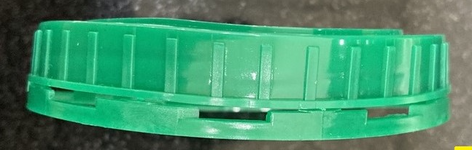
Attachments
Last edited: