voltech444
Automotive
Here is some info on this Fairchild-Caminez cam engine that I think has some potential for a modern make-over.
The Fairchild-Caminez 447 engine was a four-cylinder air-cooled radial intended for aircraft useage. It was designed by Harold Caminez, who had previously worked in the Engine Design Section of the US Army Air Service. The pistons acted on a leminiscate-shape cam, which made only one revolution for every two piston cycles, so for the same number of power impulses the engine ran at half speed. The pistons were connected by steel links to keep them pressed against the cam; the cylinder were steel with aluminium heads.
The Fairchild-Caminez 447 was first flown in an Avro 504 from Farmdale, Long Island, New York, in 1926. It was successfully endurance-tested in 1927, and was the first ever axial engine to receive a US Dept of commerce type certificate.
An IC engine expert speaks:
"Flight tests revealed what should have been predicted: a very large fourth-order torque variation due to the unusually heavy piston assemblies with their large ball-bearing rollers. Since the cam had two lobes, the second-order interia torque of the conventional 4-cylnder engine becomes fourth order in the arrangement in question. The engine was abandoned on this account."
(Quote from The Internal-Combustion Engine in Theory and Practice by Charles Fayette Taylor, 2nd edition, pub MIT press 1985, p579. This is a standard work on IC engines)
It was indeed abandoned due to vibration problems in 1929.
Stroke:
115 mm
Bore:
143 mm
Capacity:
7.3 litres
Compression ratio:
5.2
Power:
150HP at 2400 rpm
Flying weight:
164 kg (1.1kg/HP)
Output/volume:
20.5 HP/litre
I have written on physics forum for the last few years about a reverse uni-flow compression ignition 2 stroke engine. Here is some info i copied from LIM Technologies website:
"Once the LIM type engine has started, all four events occur in an only slightly modified sequence. As the power stroke ends, EXHAUST begins, then almost immediately, new air is forced into the cylinder; at the same time that exhaust continues. This new air displaces the remnants of the previous POWER stroke and COMPRESSION then takes place, completing the cycle.
The mechanical resemblance to a two-stroke is only that the piston acts as the exhaust valve. The major mechanical improvement, compared to a four-stroke, is the use of most of the head area for intake valves, since the exhaust leaves through the ports disposed around the girth of the cylinder.
The crank case, as in a conventional four-stroke, is home only to the bearings and crankshaft, the connecting rods and the main lubrication system. Another LIM advantage is that the main lubrication system has nothing to do with the valve train, although it may be involved with lubricating the compressor.
The compressor is external to the cylinder, but is vital to making a LIM type engine what it is. The compressor enables the LIM type engine to resemble a conventional four-stroke because it forces the fresh charge of air into the cylinder, and the coincidental displacement of the remains of the previous cycle.
The LIM Cycle is just three events: Ventilation, Compression, and Power. Two-stroke engines and four-stroke engines are explained in greater detail on other pages in this site."
So my idea is to take both of these designs and combine them, to make a 2 stroke reverse uniflow diesel cam engine. This Caminez cam design could work very well with some modifications. If you study the LIM engine, there is always downward force on the pistons, so the roller would always be forced down against the cam; it may be possible to remove those control arm things. The only time the pistons would not have down force is during start-up and engine braking. If the supercharger had a clutch and an electric motor it would be possible to spin the SC and create boost which would push the pistons down into place. With four cylinders, a motor like this would create 4 power strokes per revolution, not have a camshaft or pushrods, it would have a very high power density and actually be pretty simple mechanically. Could make use of new, lighter, ceramic ball bearings. SI or CI. For highest efficiency and power, a turbocharger and supercharger could be used along with water injection.
Here is another cam engine design that could also be used: The Daniel cam engine patent: US 817,905 of 17th April 1906.
This French engine by Paul Daniel of Levallois-Perret, near Paris, is the first to appear in the Cam-Engine Gallery because it was the subject of quite a comprehensive description in Model Engineer & Electrician for 28th April 1904. It is described as having been exhibited in "the last few days of the Paris salon", which possibly refers to the Exposition Universelle of 1900 in Paris, though that it would seem to indicate a pretty serious delay in reporting the fact. Perhaps some other exhibition is meant.
The report did not say if the engine was running.
There is a big roller d built into the bottom of the piston a which pushes on the top of the big elliptical cam e, and a little roller x' which bears on the inside of the cam. There is an automatic inlet valve p', and an exhaust valve k operated by rocking lever h, which is driven by an eccentric on the main output shaft; since this went round once per cycle, there was no need for a separate cam-shaft running at half engine speed.
The Daniel engine was a water-cooled four-stroke, the cam system allowing it to complete one cycle for each revolution of the output shaft. The patent shows a four-cylinder engine with two groups of cylinders and cams, and air-spring cylinders to take up the backlash in the cam system.
here is my sketch of a conventional crankshaft driven RUDIST (reverse uniflow direct-injection super-turbocharged) engine:
Link
There's more info I got I just wanted to get this up here first and i'll keep adding to it. I would appreciate your thoughts on this engine design. Thank you!
The Fairchild-Caminez 447 engine was a four-cylinder air-cooled radial intended for aircraft useage. It was designed by Harold Caminez, who had previously worked in the Engine Design Section of the US Army Air Service. The pistons acted on a leminiscate-shape cam, which made only one revolution for every two piston cycles, so for the same number of power impulses the engine ran at half speed. The pistons were connected by steel links to keep them pressed against the cam; the cylinder were steel with aluminium heads.
The Fairchild-Caminez 447 was first flown in an Avro 504 from Farmdale, Long Island, New York, in 1926. It was successfully endurance-tested in 1927, and was the first ever axial engine to receive a US Dept of commerce type certificate.
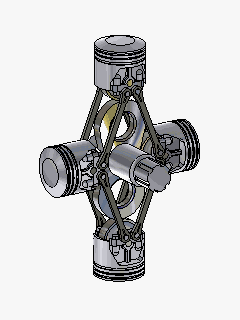
An IC engine expert speaks:
"Flight tests revealed what should have been predicted: a very large fourth-order torque variation due to the unusually heavy piston assemblies with their large ball-bearing rollers. Since the cam had two lobes, the second-order interia torque of the conventional 4-cylnder engine becomes fourth order in the arrangement in question. The engine was abandoned on this account."
(Quote from The Internal-Combustion Engine in Theory and Practice by Charles Fayette Taylor, 2nd edition, pub MIT press 1985, p579. This is a standard work on IC engines)
It was indeed abandoned due to vibration problems in 1929.
Stroke:
115 mm
Bore:
143 mm
Capacity:
7.3 litres
Compression ratio:
5.2
Power:
150HP at 2400 rpm
Flying weight:
164 kg (1.1kg/HP)
Output/volume:
20.5 HP/litre
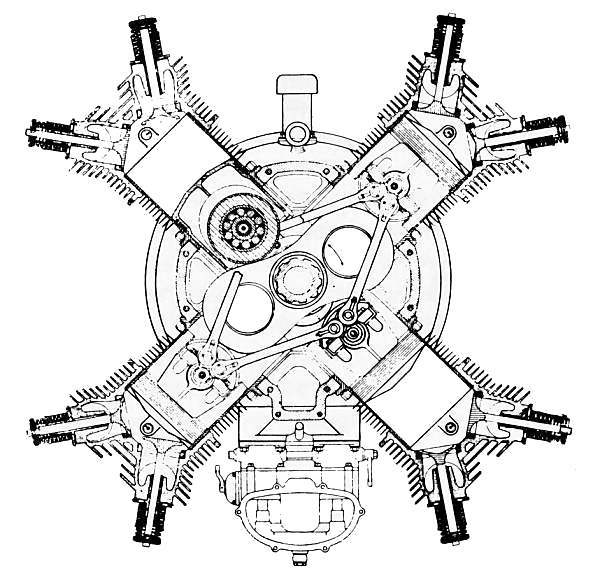
I have written on physics forum for the last few years about a reverse uni-flow compression ignition 2 stroke engine. Here is some info i copied from LIM Technologies website:
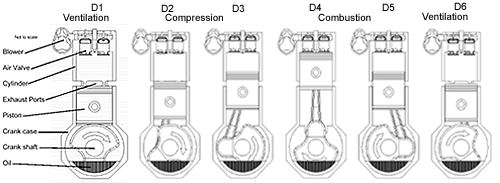
"Once the LIM type engine has started, all four events occur in an only slightly modified sequence. As the power stroke ends, EXHAUST begins, then almost immediately, new air is forced into the cylinder; at the same time that exhaust continues. This new air displaces the remnants of the previous POWER stroke and COMPRESSION then takes place, completing the cycle.
The mechanical resemblance to a two-stroke is only that the piston acts as the exhaust valve. The major mechanical improvement, compared to a four-stroke, is the use of most of the head area for intake valves, since the exhaust leaves through the ports disposed around the girth of the cylinder.
The crank case, as in a conventional four-stroke, is home only to the bearings and crankshaft, the connecting rods and the main lubrication system. Another LIM advantage is that the main lubrication system has nothing to do with the valve train, although it may be involved with lubricating the compressor.
The compressor is external to the cylinder, but is vital to making a LIM type engine what it is. The compressor enables the LIM type engine to resemble a conventional four-stroke because it forces the fresh charge of air into the cylinder, and the coincidental displacement of the remains of the previous cycle.
The LIM Cycle is just three events: Ventilation, Compression, and Power. Two-stroke engines and four-stroke engines are explained in greater detail on other pages in this site."
So my idea is to take both of these designs and combine them, to make a 2 stroke reverse uniflow diesel cam engine. This Caminez cam design could work very well with some modifications. If you study the LIM engine, there is always downward force on the pistons, so the roller would always be forced down against the cam; it may be possible to remove those control arm things. The only time the pistons would not have down force is during start-up and engine braking. If the supercharger had a clutch and an electric motor it would be possible to spin the SC and create boost which would push the pistons down into place. With four cylinders, a motor like this would create 4 power strokes per revolution, not have a camshaft or pushrods, it would have a very high power density and actually be pretty simple mechanically. Could make use of new, lighter, ceramic ball bearings. SI or CI. For highest efficiency and power, a turbocharger and supercharger could be used along with water injection.
Here is another cam engine design that could also be used: The Daniel cam engine patent: US 817,905 of 17th April 1906.
This French engine by Paul Daniel of Levallois-Perret, near Paris, is the first to appear in the Cam-Engine Gallery because it was the subject of quite a comprehensive description in Model Engineer & Electrician for 28th April 1904. It is described as having been exhibited in "the last few days of the Paris salon", which possibly refers to the Exposition Universelle of 1900 in Paris, though that it would seem to indicate a pretty serious delay in reporting the fact. Perhaps some other exhibition is meant.
The report did not say if the engine was running.
There is a big roller d built into the bottom of the piston a which pushes on the top of the big elliptical cam e, and a little roller x' which bears on the inside of the cam. There is an automatic inlet valve p', and an exhaust valve k operated by rocking lever h, which is driven by an eccentric on the main output shaft; since this went round once per cycle, there was no need for a separate cam-shaft running at half engine speed.
The Daniel engine was a water-cooled four-stroke, the cam system allowing it to complete one cycle for each revolution of the output shaft. The patent shows a four-cylinder engine with two groups of cylinders and cams, and air-spring cylinders to take up the backlash in the cam system.
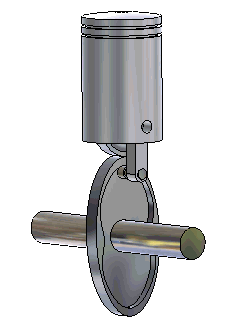
here is my sketch of a conventional crankshaft driven RUDIST (reverse uniflow direct-injection super-turbocharged) engine:
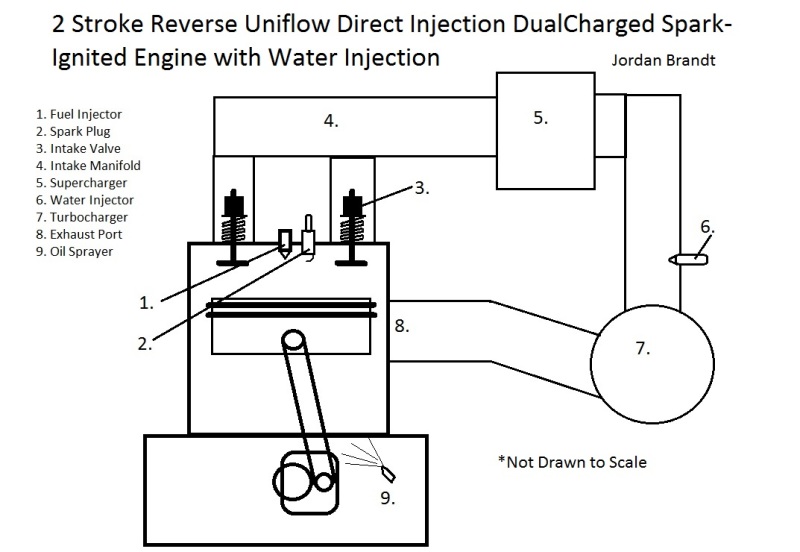
Link
There's more info I got I just wanted to get this up here first and i'll keep adding to it. I would appreciate your thoughts on this engine design. Thank you!