BSVBD
Structural
- Jul 23, 2015
- 463
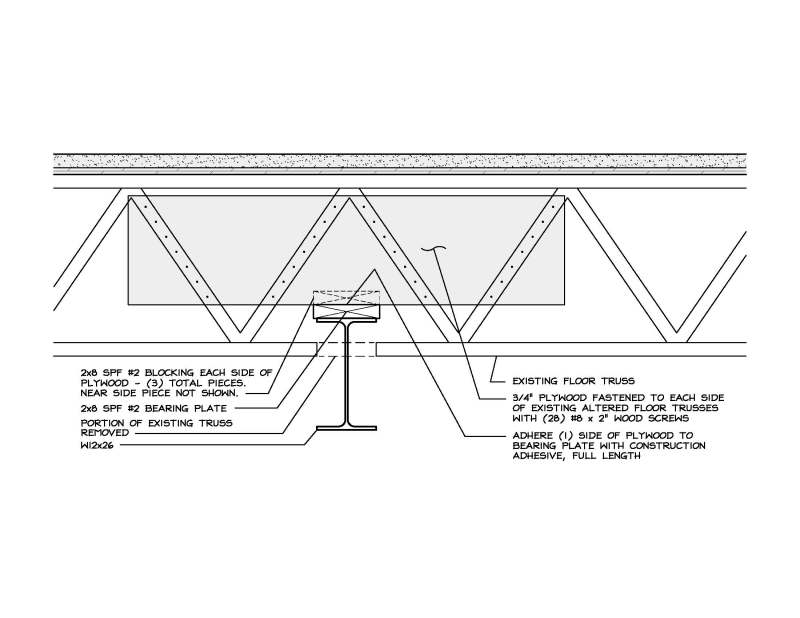
The contractor removed a portion of the bottom chord of the floor truss in order to install the steel beam. (This W12x26 supports another steel beam which is neither shown, nor applicable to this detail and the problem at hand.)
NDS Table 11.3.2B provides Dowel Bearing Strength of Plywood.
Can i use that same bearing strength as in compression parallel to have the vertical plywood member bearing on a wood bearing plate, similar to the physical load path of a TJI? Please see detail above.
Any other suggestions?
Thank you!